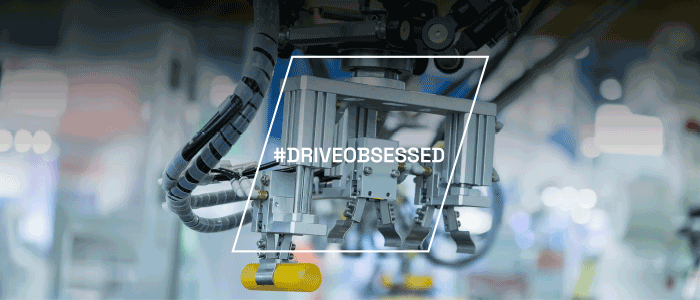
Ooops! Page not found
We're sorry, but the page you're looking for can't be found at the moment.
Our engineers and technicians are on it...don't worry..the page will be up and running in no time.
Whilst we're working on fixing the page, you can visit one of the following links or Contact Us if you're still not finding what you are looking for.
Thank you for your patience!
Home Page
Products
Downloads
Contact Us