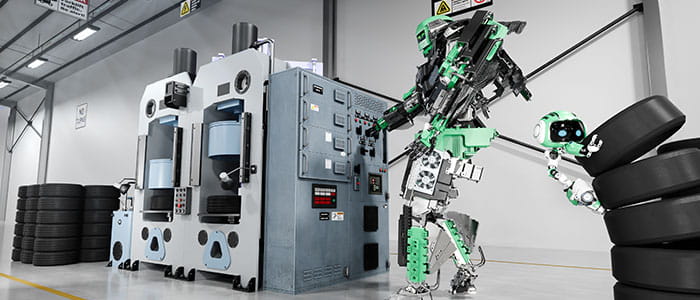
Rubber and plastics
Easily integrated, providing productivity gains and energy savings
- Overview
- Downloads
Control Techniques' drives are used in nearly every rubber and plastics application where electric motors are found, providing outstanding reliability, performance, safety and economy.
Control Techniques' drives guarantee easy integration and increased throughput, as well as significant cost savings.
For more information on plastic extrusion applications see our Rubber and Plastics Case Studies page.
Key benefits
- Providing precision and repeatability in terms of performance, control and long term reliability from machinery
- Maximizing productivity and throughput
- Saving energy
- Reducing operations costs
- Providing the support and technology to exactly meet your production requirements
- Enhancing safety and providing environmentally sound solutions
Typical applications include
- Extruders
- Compounding
- Mixing
- Pullers
- Core Pulling
- Slitters
- Web Handling
- Dual-turret winders
- Feeders
- Heat Sealers / Perforators
- Re-spoolers
- Rotary Knife
- Flying Shear