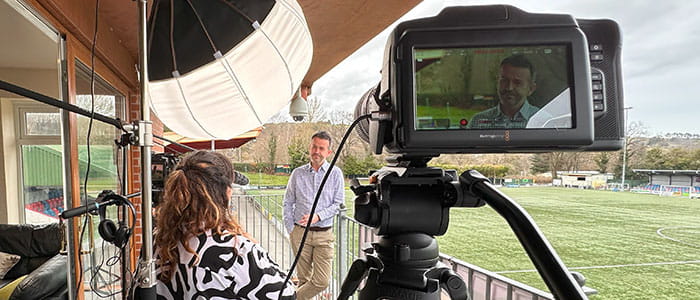
-
25 avril 2025
En reconnaissance de son récent travail d'unification de ses marques constitutives et d'harmonisation sous une identité visuelle Nidec rafraîchie, le magazine Transform a décerné à Nidec les prix d'or et de diamant de la meilleure architecture de marque lors des Transform Awards Europe.
-
03 avril 2025Nidec Drives a le plaisir d'annoncer la nomination de Laurent Babaud au poste de président.
-
26 mars 2025TOMRA, leader mondial de la distribution automatique inversée, a dû relever un défi lorsque les Pays-Bas ont étendu leur système de consigne aux boîtes de conserve.
-
04 novembre 2024Nous apportons un changement révolutionnaire à notre programme de garantie. Dès à présent, nos clients bénéficient d'une garantie standard de 5 ans sur tous les variateurs, modules optionnels et claviers de Nidec Drives.
-
23 octobre 2024
-
09 octobre 2024
-
28 août 2024Dans le vaste catalogue de solutions de Control Techniques, Trinca a profité des servomoteurs Unimotor HD haute dynamique et des servovariateurs Digitax haute performance, pilotés par les contrôleurs de mouvements MCe et MCz.
-
06 août 2024
Delve into the cutting-edge world of HVAC efficiency through the lens of permanent magnet motors.
-
09 juillet 2024Dans le cadre de l’engagement de Nidec Drives dans le développement des variateurs, le Commander S de Control Techniques est désormais livré avec un capot cache bornier, installé en usine en tant qu’équipement de série.
-
06 juin 2024Dans le cadre de l’évolution continue de la technologie des variateurs Nidec Drives, le nouveau module optionnel SI-BACnet IP de Control techniques offre un contrôle amélioré et une efficacité optimale des systèmes tertiaires, en garantissant un fonctionnement précis et coordonné pour maximiser le confort des occupants.
-
31 mai 2024The Secretary of State for Wales and Conservative candidate for Monmouthshire, David TC Davies, and Craig Williams, Conservative candidate for Montgomeryshire, have today (30th May 2024) visited the Nidec Drives UK Manufacturing Site, based in Newtown, Powys.
-
16 mai 20242023 saw Nidec Drives host a series of events in celebration of their 50th anniversary. The purpose of the events was to give back to our employees, whilst also contributing to the wider community.