In this post, industry expert Andy Pye asks if Industry Vier Punt Nul is the same as Industry 4.0.
Industry is one of the pillars of the European economy, accounting for 15% of value added (compared to 12% in the US). It serves as a key driver of research, innovation, productivity, job creation and exports. Industry generates 80% of the EU’s innovations and 75% of its exports. The manufacturing sector in the European Union accounts for 2 million enterprises, 33 million jobs and 60% of productivity growth.
However, it now faces new challenges: new market players, from Asia in particular, have undermined the competitiveness of European countries and led to significant job losses in established markets – Great Britain (-29%), France (-20%), and Germany (-8%).
Western civilisation has already witnessed three industrial revolutions, disruptive leaps in industrial processes resulting in significantly higher productivity. The first was the use of hydropower, the increasing use of steam power and the development of machine tools. The second brought electricity and mass production. The third and most recent further accelerated automation using electronics and IT.
The fourth industrial revolution is already on its way. This time, physical objects are being seamlessly integrated into the information network. The Internet is combining with intelligent machines, systems production and processes to form a sophisticated network. The real world is turning into a huge information system.
At the last SPS, the German automation show held every autumn in Nuremberg, it would be easy to form the opinion that the Internet of Things (otherwise known as Industry 4.0, or the IoT) is thriving. But in the UK, it is generally being viewed with a mixture of excitement and trepidation.
Industry 4.0 emphasises the idea of consistent digitisation and linking of all productive units in an economy. Based on new and radically changed processes in manufacturing companies, data is gathered from suppliers, customers and the manufacturing company itself and linked up with real production. 3D visualisation will improve the design of more complicated production layouts and technologies like collaborative robots that enable more flexible manufacturing. Integrated networks of sensors coupled with actuators, data federation, big-data analytics, and fast autonomous decision-making will change the world.
Today, there are some daunting technical problems to overcome, among them incompatible front-end device connection protocols, the management of billions of intelligent endpoints, low-cost/low-volume data transmission options, security issues and business models. But all these technical and business problems are solvable and companies already exist with solutions. Above all, German industry is well advanced and prepared and SPS was bulging with IoT-ready technology.
Industry 4.0 and its benefits for manufacturers
In contrast, and coinciding with the third and final day of SPS, an event entitled “From Industry 4.0 to Digitising Manufacturing – an End-User Perspective” took place at the Lloyds Bank Advanced Manufacturing Training Centre on the MTC campus at Ansty Park, Coventry, aimed at explaining Industry 4.0 and its benefits for manufacturers.
About 150 European engineers, business people and academics heard how digitised factories will be developed in Britain and across the world, in a more collaborative, connected way.
Given the leading position adopted by Germany, it was fitting that the opening address was given by Dr Peter Ammon, the German Ambassador to the UK. Ammon said that manufacturing accounts for 22% of GDP in Germany, employs 15 million people, and is a major driver of her exports, but that Germany could not rest on its laurels. “Making digital information and communication technology usable for industry will be key to maintaining our competitiveness internationally. 80% of German businesses think their value chain will be substantially digitised by 2020,” he said.
But according to The MTC’s Dr Lina Huertas, many UK manufacturers are failing to see the same business benefits: “Many manufacturers in the UK don’t know what Industry 4.0 means, or understand its potential impact on industry, and they don’t know how to respond to the technological implications,” she argued. “The conversation has been
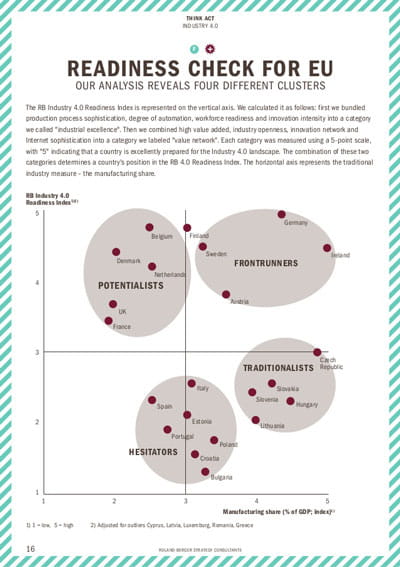
dominated by the technology and software providers and the manufacturers feel they have been left out. They don’t see the benefits, they fear the risks, and they don’t know who to turn to for reliable information and support.”
Henning Banthien of the German organisation Platform Industrie 4.0, an innovation hub designed to provide support “for the coordinated and organised transition into the digital economy in Germany” recognised that making digital information available for manufacturing is key in the German economy. Special attention is being paid to the small and medium enterprise (SME) community, which is seen as key to the success of the project. Of course, the demographics of the SME bedrock in Germany is somewhat different to that of the UK, in that it comprises largely family-owned businesses.
In contrast, UK SMEs are often based on start-up finance, disparate shareholdings, venture capital and are often susceptible to takeover at an early stage in their lives. But even so, the SME community in the UK has an outstanding reputation for innovation, as evidenced by inventions from the hovercraft to graphene, to name just two. And despite relatively low public funding for R&D compared with other countries in the OECD group of mostly wealthy nations, the UK this year maintained its second place in the global innovation index.
At a time when Britain’s membership of the EU hangs in the balance, Anne-Marie Sasson from DG Connect put forward the European Commission’s view that every industry in Europe should have access to the latest technologies and that there should be a digital innovation hub in every region. She highlighted a key message (Fig 1) which plots an Industry 4.0 “readiness index” against manufacturing’s share of GDP. Countries are divided ito 4 groups, with Germany shining as a frontrunner, along with Ireland, Sweden and Austria. The UK falls into the “Potentialists” group, along with Norway, Netherlands, Denmark, Belgium and France. Other European countries are grouped into Traditionalists and Hesitators.
Sasson believes that for the European Union to maintain its competitiveness, keep a strong industrial base and manage the transition to a smart industrial and services economy, digitisation of all sectors will be needed. 75% of the value added by the digital economy comes from traditional industries, rather than ICT companies. The integration of digital technology by those traditional businesses is currently the weakest element.
But the target for Europe to reach 20% manufacturing share of GDP for its industry is sending the message that Europe’s future depends on manufacturing. In the future, quickly switching over to Industry 4.0 will be a major competitive advantage for an economy over its global competitors. Europe as a whole is in good shape to embrace the new industrial world.