Few things can damage the financial stability of a manufacturing facility more than unexpected downtime. On average, manufacturers suffer with 30% or more downtime during their scheduled production time. In some industries, such as automotive assembly, downtime can cost up to £17,000 per minute (a mind-blowing £1 million an hour). Some unplanned downtime may be beyond the control of a manufacturer – caused by infrastructure failures, human error or even natural catastrophes. However, there are ways to reduce the risk.
Automated machinery can dramatically increase effectiveness by speeding up production time and reducing the potential for human error, therefore increasing overall equipment effectiveness (OEE).
According to the Annual Manufacturing Report 2017 by Hennik Research, two-thirds of UK manufacturers have made investments in automation in the past 12 months. However, once the investment has been confirmed, the installation of automation into production needs to run smoothly.
Traditionally, maintenance has been done on a fixed schedule, replacing items at constant intervals. Although the intervals are usually based on established knowledge, that is only part of the story – as we all know, parts wear out at different rates for all kinds of reasons. Constant intervals do not take into consideration the unique and varying circumstances of a machine being maintained. So although general purpose schedules are easy to manage by arranging for spares to be delivered in a predictable manner, they risk wasting money by replacing parts that are still operational.
On the other hand, predictive maintenance is about getting the most life out of equipment while minimising the risk of failure. It ensures that parts are used to the end of their natural life, but risks downtime due to delays in delivery of replacements or additional costs due to higher stock levels. The ideal combination is predictive maintenance with just-in-time supply chains.
Predictive and Preventative/Preventive Maintenance are terms that are often used interchangeably, but they should not be. Preventative Maintenance tasks are completed when the machines are shut down and Predictive Maintenance activities are carried out as the machines are running in their normal production modes. But both benefit from modelling the process of part replacement.
A preventative maintenance program will usually comprise five key areas, covering equipment, measurement, inspection, data management and action protocols. The cost and complexity of the program will always depend on the critical nature and cost of the machinery and or downtime impact.
Instruments for condition monitoring will look for variances in acoustics, vibrations, thermal output, motor current signatures and other areas, which help determine maintenance schedules and reactive steps needed to keep machinery running optimally.
The process involves gathering large quantities of data – such as maintenance records and data from sensors on the equipment. Collecting and archiving company-wide production data is hugely beneficial, but can be difficult to obtain. Additional data sources such as sensors on the equipment will also be important to build the big picture.
One of the biggest challenges is gathering and interpreting so-called unstructured data, such as free text in maintenance records, design specs, test data from failed equipment, or even comments on social media or Google searches.
Having collected all the data, the next step involves using data analytics to make sense of the data. Investments in automation have generated a significant increase in the deployment of automation software on the factory floor. Traditionally, SCADA applications were simply a way to acquire data from machinery. However, modern automation software applications can provide much more intelligent insight. The most intelligent data analytical automation software will also provide graphical visualisation of production data and generate customised statistical reports.
After that, defining rules becomes the basis for a tentative preventative maintenance model. For example, pattern recognition can also discern the relationships between certain types of events and machine failures. Once the model
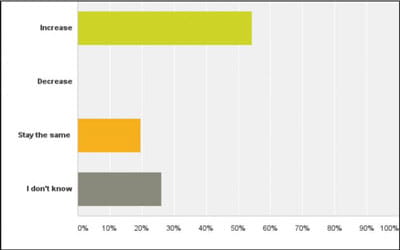
is built, it must be tested and progressively refined. But a bad model is better than no model, albeit only marginally, but with progressive refinement via a continuous learning loop, the model can be progressively updated.
According to a recent survey, conducted by test and measurement company HBM, video use is accelerating in data collection. The study shows that almost half of the respondents (47%) already use video in data recording today, while 54% of the respondents expect video use within their organization to increase in the next year.
Video cameras are already used in many test and measurement applications throughout the industry in addition to data collection with traditional tactile sensors. But until now, there has been very little information on the level and nature of this use.
“Based on the study, there is no longer any question that recording video data in parallel to tactile sensors or digital bus signals is becoming more and more attractive to users,” says Christof Salcher, Product Manager Instrumentation at HBM. “Video supports traditional sensor data and is becoming a valuable source of additional information, making the room for interpretation even narrower in testing.”