What is a servomotor?
A servomotor is a rotary or linear actuator designed for precise positioning, velocity and acceleration. They’re ideal for many applications; from simple DC servomotors used in toys, to modern AC servo variants which are common in automation control, robotics and electric vehicles. The servomotor has gone through many developments to get to where it is now, each revision enabling other technologies, such as industrial automation, to thrive.
Where the servomotor began
The first servomotors were permanent magnet DC. They provided a straightforward method of torque control made up of a cage containing a fixed magnet and rotating windings within. Unfortunately, this design was not without its problems. To transfer electricity, spring loaded carbon ‘brushes’ press up against a commutator (which transfers power to the windings). As the brushes wear, debris is left behind. This eventually causes a build-up, ‘arcing’ the commutator strips which shorts the motor. As a result, DC brushed servomotors require monthly maintenance to prevent motor damage. To help reduce the cost and risk of running a brushed servomotor, engineers developed the brushless servo system.
Enter the brushless servo system
The first type of brushless servo system emulated the brush-type DC servo motor. They used three-phase permanent magnet motors and electronically ‘commutated’ the current from one pair of motor windings to another. To monitor velocity an encoder and brushless tachometer was added. This new brushless design meant motors would last longer between servicing.
Constraints drive further innovation
The original brushless design was limited to low power applications. This led to the development of the AC servomotor using a permanent magnet motor with sinusoidal back EMF (created by using skewed magnets and overlapping windings) also known as field-oriented or vector control.
AC servomotors are commonly used in today’s industrial applications. It’s ideal for higher powered systems or where operations require smooth torque. AC servo motors work by using a split ring commutator with the two sections wired to opposite poles of the motor. The alternating field causes the poles of the windings to change polarity, turning the motor.
Demand for efficiency in motor control
Servomotors can be up to 95% efficient at full power and have a low power density as there is no rotor current, meaning the motor can produce 100% torque instantly. It is for this reason that electric cars feature servo motors.
Although the focus has previously been placed on the servomotor itself, much of the improved performance comes from the encoder. This device creates an accurate snapshot of the rotor position. Different encoders have varying ‘resolutions’, a higher resolution means the motor will stop more accurately.
Servo motor used today has changed from the early generations. Now they are made with the latest magnet technology and connected to variable speed drives which give them performance that is hard to match.
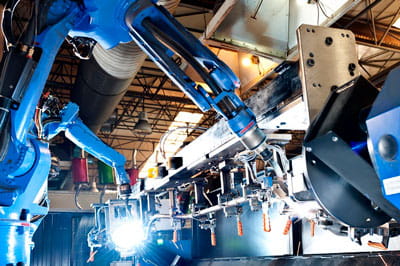
A tale of two motors
There are two types of servo motor used in industry today: linear and rotary. Both have advantages. With a linear motor, you’ll benefit from:
- Higher speeds
- Higher accelerations
- Direct drive
- Practically no wear
- High position accuracy
It might seem that linear motors have all the advantages, but there are many applications which only use a rotary servo motor. This is because linear motors heat up; a by-product of wasted energy. The heat generated causes thermal growth, which effects the load, bearings, grease and sensors. Over time this negatively impacts on the lifespan of components. In addition, thermal growth is likely to cause issues with binding and increased friction.
Rotary motors have the following benefits:
- Continuous duty
- Reversible
- Speed is proportional to the applied voltage
- Torque is proportional to the current
- Very efficient
However, the reality is that rotary and linear motors are used for difficult application setups. For instance, rotary servo motors are used with woodturning mechanisms (lathes), industrial spinning, weaving machines, looms, and knitting machines. Linear servo motors are used with short-move pick and place and inspection equipment, longer moves and flying shear applications, roller coasters, people movers, and vehicle launching systems.
In conclusion
Servo motors can offer higher performance, faster speeds, and smaller sizes than induction motor systems. Additionally alongside variable frequency drives servomotors can use 30% less energy in positioning applications.
Conversely induction motor systems (lower cost, rugged, reliable, and well known) can offer an alternative to servo motor systems for certain applications. This, of course, is based on similar electronic controls being used (with the latest technology and approximately the same cost), leaving the cost of motors the differentiating issue.