Public electricity supplies are generally reliable, but they do suffer disturbances. Obviously a total loss of supply results in all electrical equipment stopping, unless it has a backup supply such as a UPS and/or backup generator connected. When the power returns the equipment re-starts from the off state in the way it was designed to start. However there is a class of disturbances which takes the form of short interruptions or voltage dips where the behaviour is not so obvious.
Short voltage dips are not uncommon. They can be caused by line faults triggered by lightning or falling objects such as trees etc. Whenever a fault occurs in the public power system a voltage dip propagates from the fault point around the whole system. The power company protection gear trips the faulty circuit on a timescale in the region of 200 ms, after which power recovers for most consumers, sometimes after several attempts by auto-reclosing circuit breakers. However during this time power consumers experience voltage dips of various depths depending on their electrical distance from the fault. In heavy industry, voltage dips also occur when starting large motors direct on line.
It is important for electrical equipment to behave correctly during and after a dip or interruption, a matter which is easily overlooked. It should ride through a short or shallow dip. If this is not possible, the correct behaviour depends on the application. in some applications the equipment must stop and wait to be re-started, either manually, to avoid a hazard from unexpected starting, or automatically but under coordinating control for multiple motors. Other applications need the equipment to re-start automatically when the power returns, in a controlled manner. Failure to re-start correctly can cause lost production in manufacturing plant, emergencies such as people stuck in lifts, air-conditioning systems tripping, and all kinds of electronic devices needing an expensive service visit to reset them.
Dips and interruptions
The shortest dips and interruptions are typically about 10 ms, or one half-cycle of mains, in duration. Anything exceeding about 10 s would be considered a power loss. The range of durations where we need to look closely at behaviour is primarily from 10 ms up to about 500 ms. In this range, design errors can result in incorrect behaviour such as processors hanging or crashing, or data being corrupted.
In a three-phase system faults often affect only one phase, since lightning and falling objects often only affect one phase. The fault may however spread to all three. A single phase-to-ground fault in the high voltage transmission system appears as a line-to-line fault in the low voltage distribution system, after the delta-star transformers. Dips from motor starting affect all three phases.
Energy storage and ride-through
In a typical mains-powered electronic circuit there is a fairly large capacitor connected in the internal DC supply line to smooth the rectified voltage, and it usually stores enough energy to keep the circuit running for around 10 ms to 20 ms. For shorter dips or interruptions it continues to operate normally, and there may be a power monitor circuit which detects a low voltage. There is then time to run a short routine to save some essential data in the non-volatile memory and put the system into a known state, from which it can restart once the power supply returns. If ridethrough up to about 100 ms is required then this can be achieved by adding extra capacitance, beyond which some kind of battery or UPS would be required.
In a typical variable speed drive, because of the high power throughput the capacitors do not store enough energy to supply the rated load power even for 10 ms. There is no realistic possibility to ride through the dip in a simple way by using the capacitor stored energy, unless the load power happens to be very low at the time. In some special applications additional external capacitors, super-capacitors or batteries have been connected to the DC bus to ensure ridethrough, but this is usually too expensive.
On the other hand, there may be some useful energy stored mechanically in the motor inertia. Depending on the application, it may be possible to use some of this energy to keep the drive in a viable state ready for when the power returns.
Ride-through for drives
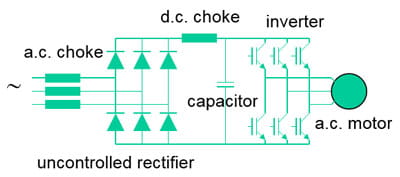
Figure 1 shows the main power components of an AC drive. The chokes are optional and have little effect on ridethrough.
The rectifier is unidirectional, power can only pass from the AC supply to the DC bus. The inverter and motor are bidirectional, so it is possible for energy to return from the motor to the drive DC bus, provided there is also enough energy to keep the motor magnetised.
The drive controller has a measurement of the DC bus voltage, so it can detect a drop in voltage. A short interruption of the AC supply has the same effect as a dip, since the DC voltage falls as the capacitor discharges. There are several possible situations, and the detailed behaviour depends on the motor control mode being used. Let us consider a simple open loop control with basic fixed V/f ratio.
In any case where the voltage recovers before the supply loss detection level is reached, normal running then continues. There is a short surge of input current as the capacitor re-charges without the benefit of the soft charge circuit. The drive is designed to withstand this surge without harm, but it has been known for circuit breakers to operate in this situation, especially where a number of drives are fed from the same breaker.
Supply loss routine:
There is a user-selectable mode parameter which gives the choice of three actions, which can be chosen to suit the needs of the application:
1. No action (supply loss function disabled)
2. Ramp to stop
3. Ride through
In option 1 the motor coasts to a stop. The drive performs no action when the voltage drops below the supply loss detection level. If the voltage continues to fall to below the under voltage detection level, the drive is disabled and the motor coasts to a halt. If the power returns the drive executes an automatic restart if the enable and run commands to the drive are still present.
Option 2 would normally be selected where the application requires multiple coordinated movements and it is important that the drive should not attempt independent actions. The motor is ramped to a stop when the voltage drops below the supply loss detection level. If the power returns while the drive is decelerating the motor, the drive continues to ramp the motor to a halt, otherwise the drive enters the under-voltage state and shuts down.
There is a difference in detailed behaviour between some Control Techniques products once the drive reaches a stop if the supply has returned:
- For Unidrive M700 and related products: Once the motor has reached a stop, the drive enters the disabled state and requires the enable signal to be toggled before it can run again.
- For Unidrive M100 to M400 and related products: Once the motor has reached a stop then as long as the enable and run commands are still present the drive restarts and ramps the motor speed back to the speed reference.
Option 3 would normally be selected where the application requires the drive to continue in independent operation as far as possible. The drive reduces the motor speed setting in a controlled fashion so that motor flux is maintained and mechanical stored energy in the motor and load is returned to the drive as the speed falls. The energy is used to maintain the motor magnetising current and to supply power to the control circuit of the drive. If the power returns before the energy is exhausted then the drive accelerates the motor back to its set speed.
The chance of successful ridethrough clearly depends on the mechanical loading at the time and the specific inertia of the motor and its load.
Note that if the voltage dip occurs in only one phase of a three-phase supply then the recovered energy has only to “fill the gaps” for the rectifier during the missing phase voltage intervals, which requires much less energy than for a three-phase dip and is most likely to result in successful ridethrough.
Limit to number of auto-reset attempts
This can be set to a desired number or unlimited.
Spinning motor restart:
In all of these options, if automatic restart is selected then it must be considered whether the “catch a spinning motor” routine is required. Where the drive has maintained control of the motor, i.e. in a ramp or ride-through state, this is not necessary. However once the under-voltage trip has occurred the motor is no longer controlled. It may continue to spin as a result of its inertia and/or external factors such as air flow in a fan. In that case the re-start might fail unless the spinning motor algorithm is enabled.
Standards and requirements for power dips, interruptions and ridethrough
There are international and EU harmonised standards for immunity of electrical products to power dips and interruptions. In the EU this is covered legally by the EMC Directive. In the rest of the world it is generally considered a matter of product quality rather than EMC law. For equipment rated below 16 A per phase the test standard is IEC 61000-4-11 (EN 61000-4-11 in the EU), but this standard gives a wide range of optional test levels and no pass/fail criteria. The product standard has to be consulted to find the precise requirements. A typical requirement can be taken from the generic immunity standard for industrial equipment, IEC 61000-6-2:
The equipment has to operate as specified during the dip and afterwards, and no loss or corruption of stored data must occur. Note that this does not require literal ride-through, in the sense of continuing to supply rated output power, but only operation as intended. The purpose of the test is to find errors or bugs such as hung states or corrupted stored data following the dip/interruption. If the test is applied to a machine which incorporates drives then the drives must be correctly configured to ensure that the complete machine behaves as intended during and after the dips.
For equipment rated at over 16 A per phase there is another test standard IEC 61000-4-34. This standard is little used, because of the difficulty and cost of the test equipment. The behaviour of a high power drive can be predicted reliably by simulation and by scaling from a lower power model.
Another standard for power disturbances comes from the Information Technology Industry Council (ITIC) in the USA and is sometimes specified for IT equipment. It does not define a test method but only a terminal voltage behaviour. The ITIC curve (previously CBEMA curve) shows continued operation for interruptions of up to 20 ms. It only applies for single-phase supplies and does not readily adapt to three phases.
From the previous discussion you can see that a drive may be able to achieve this in ridethrough mode provided sufficient stored energy can be recovered by decelerating the load, particularly with a three-phase supply.
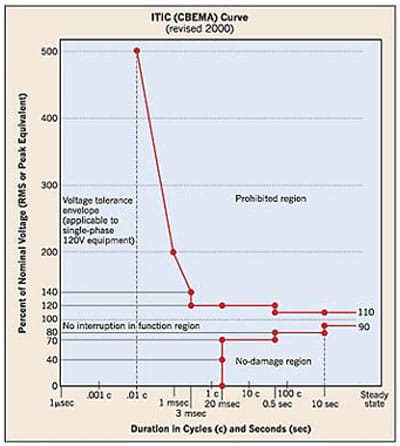
Browse all Technical blog posts