
Depending on where you are, modern factory communications protocols can have different titles. Here, Joseph Walker, content manager at Control Techniques, discusses some of the key differences.
Anyone who works in manufacturing will have read articles by politicians and commentators about how manufacturing could end the economic crisis by creating thousands of high-tech, high-productivity jobs. These articles usually reference ‘Industry 4.0’ and the ‘Industrial Internet of Things’. If you work in Asia, you may be familiar with ‘Made in China 2025’. The common thread in all these titles is that they concern the use of data.
These terms represent attempts by various governments and industries to help their manufacturers meet the challenges of the future. Below is a quick guide to what they mean and why they’ve been created:
Industry 4.0
Industry 4.0 was originally conceived by the German government, and has been defined by Chancellor Angela Merkel as “connecting digital technologies with industrial products and logistics”. The phrase Industry 4.0 is now becoming widely used across Europe.
Essentially Industry 4.0 is about industry harnessing the power of the internet and big data to radically improve productivity and flexibility. For example it is often touted as a way for factories to achieve ‘mass customization‘ – so that customized bespoke items can be produced at the high volumes and low costs associated with mass manufacturing.
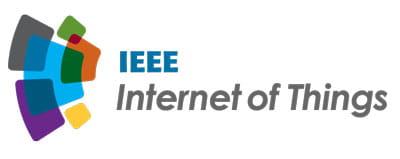
The industrial internet of things
The Industrial Internet of Things is viewed as a subset of the Internet of Things. The Internet of Things is defined by LNS, a US based industrial research organisation, as networks that “connect people, processes and things to enable new cyber-physical systems”. The classic example is the fridge that is able to tell when it has run out of milk, and can order more online automatically. The Industrial Internet of Things is an American concept, but applied specifically to industry.
So it is really just geography that differentiates Industry 4.0 and the Industrial Internet of Things. But Made in China 2025 is quite different, although it is often mentioned in conjunction with the other two.
Made in China 2025
Made in China 2025 has been conceived because the Chinese manufacturing sector is under pressure from increasing international competition from developing countries, as well as decreasing global demand. The concept is very important to the Chinese government because manufacturing makes up such a huge share of Chinese GDP. Indeed, Chinese factories
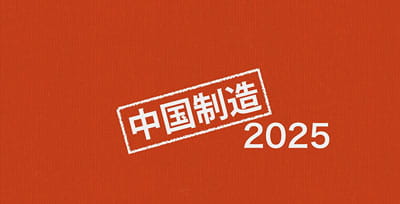
currently produce about 20% of the world’s manufactured goods.
Made in China 2025 is actually a ten year plan focusing on ten specific industries: information technology, industrial automation, aerospace, maritime, rail, energy efficient vehicles, power equipment, agriculture, new materials and biotechnology. The plan identifies five clear, achievable projects to help these industries, such as “establishing a manufacturing innovation center”
The Economist has reported that the immediate aims of Made in China 2025 are “to improve quality, productivity and digitisation, and to expand the use of numerically controlled machines”. The magazine also noted that these things are “in common use by world-class manufacturers in other countries”. In other words, Made in China 2025 is a plan for how Chinese manufacturers can catch up technologically with Western manufacturers. In this respect it is much more limited and achievable than Industry 4.0 and the Industrial Internet of Things. Ultimately, Made in China 2025 will be followed by two more ten year plans that aim to transform China into a “world manufacturing power”.
So why are governments so keen to help manufacturers?
The reason that governments are so active is that, as a sector, manufacturing provides benefits out of all proportion to its size. For example, according to a recent UK government briefing paper, UK manufacturing amounts to only 10% of national economic output, yet accounts for 44% of UK exports and 70% of total UK research and development spending.
Manufacturing also tends to offer much higher productivity than other sectors. In 2014, manufacturing productivity grew by 3.4%, whilst productivity for the economy as a whole grew by only 0.2%. In his book, The New Industrial Revolution, Peter Marsh, the Financial Times’ former manufacturing editor, describes manufacturing workers as “economic shock troops” and says “one person in a manufacturing job has delivered more economic benefits than people in other sectors”.
This is one reason why UK chancellor George Osborne has called for a “march of the makers” to rebalance the British economy away from services and towards manufacturing.
Of course these benefits don’t apply only in the UK: manufacturing firms across the world enjoy inflated benefits when compared to other sectors of the economy. And that is why governments around the world are investing so much money and time on concepts like Industry 4.0, the Industrial Internet of Things, and Made in China 2025.
It’s perhaps worth examining how these modern manufacturing protocols are applied in a real life setting. Consider the printing industry; in the past this industry was based on a process called type setting. To create a new printed document the type setting process was manual and laborious. It made sense to print large volumes of everything and store them until they were all sold, and then do it over and over again. This improved when the type setting was digitized, but still high volumes were required for the process to be economic. Management and maintenance of the press was a highly skilled job, and managing the logistics to ensure you had the right consumables in place took a team of people whose performance was vital to successfully running the business.
The introduction of digital printing for personal computers found new applications for labels and other documents where every sheet of paper can be unique, however this was used in low volume or specialist applications as there was a severe penalty on speed or quality.
Nowadays, digital printing has vastly increased in speed and is applied to an ever-widening array of print applications. The key benefit of digital printing is that every single page can be unique so it costs the same per item to print one off as to print 10,000 copies.
One of the applications where this has famously been applied is on the “Share a Coke” marketing campaign, where each Coke bottle has one of the country’s top 250 names randomly selected and printed on the front. Clearly each country has a different list of names, adding further complexity. Not a problem using this new procedure though. And, if your name is not included don’t worry, you can order your personalised bottle directly from Coke.
Another application allows publishers to continue to sell specialist or low volume books that are out of mass print by digitally printing them to order one at a time. At the beginning this technology was only economic for fairly small print runs, however, as the technology improves it begins to be economic in far greater print runs, rivalling traditional print technologies.
The concept could go further, because the printing press is connected to the internet, it facilitates business model innovation. The traditional business model for a print press manufacturer was to sell the press and hope to sell the ink. IoT allows the print manufacturer to charge their customer based on the number of pages printed and the types of content on those pages, allowing the manufacturer to appropriate some of the additional value their customer is getting through the use of their machine. In this business model, the print manufacturer supplies all the consumables as part of the page costs.
The print press accurately predicts when replenishment is required and can automatically re-order inks, paper and any other consumable materials. The manufacturers of the consumables also know exactly how much ink is being used in real-time and when the printer is likely to need replenishment allowing them to accurately plan and optimise their manufacturing and logistics processes.
Maintenance visits can also be automatically scheduled based on usage and data collected from the many sensors that are connected across the press. The data could be sent digitally to the print manufacturer who can consolidate it with data from many presses over many years. This creates a rich data source that can be analysed to identify important patterns and insights, such as how to optimise print speed, identify factors that can impair print quality or to predict a part failure in the machine and schedule preventative actions.
When a technical problem does occur, experts remotely access the digital printing press and perform fault finding operations, potentially saving them money.