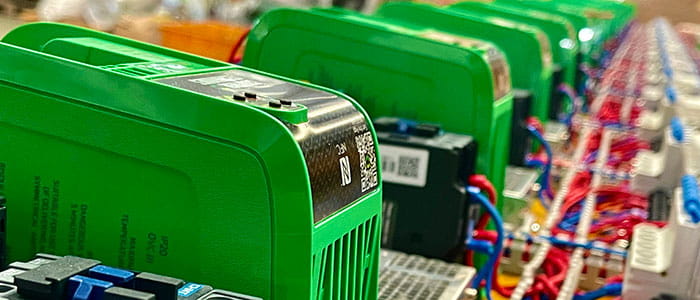
Alimenti e bevande
Cosecha de miel
Commander C garantisce una smielatura automatica delicata
Gli azionamenti controllano le macchine slitter
Control Techniques nel cuore delle macchine slitter a elevata potenza
Digitax boosts performance by 30% at Italian food packaging plant
Improved throughput and quality
HVACR
Migliore esperienza per il cliente
Eliminate le forti vibrazioni nella sala bowling a londra
Lavanderia
Rapide rotazioni risolvono la situazione
Rapide rotazioni risolvono la situazione per il produttore di pannelli per controssoffitti
Machine Control
Aumento dell’efficienza in Nidec Drives
Un caso di studio di automazione manifatturiera avanzata
Movimentazione materiali
Rivoluzionare il processo di riduzione dei rifiuti da imballaggio
Nidec Drives e l’economia circolare
La movimentazione di rinfuse favorisce la qualità delprodotto
Gli azionamenti Unidrive M400 e M701 di Control Techniques consentono di raggiungere più tonnellate per metro quadrato di qualsiasi altra attrezzatura per movimentazione di rinfuse
Innovative companies need innovative suppliers
Variable speed drives achieve weight accuracy of 0.025%
Compressor boosts performance
Efficient drives process 120,000 tonnes of waste per year
Metalli
Controllo servo in un ambiente sotto vuoto
Unidrive M700 assicura il controllo della posizione in un ambiente sotto vuoto
Imballaggio
Future-ready labeling technology
Digitax maximises throughput with precision motor control
Imballaggio Perfetto
Unidrive M700, Digitax HD e Commander C300 per prestazioni ai massimi livelli e risparmio energetico con ottimizzazione del flusso di aria
Portare al successo
Azionamenti Unidrive M700 la partnership con Control Techniques si è rivelata vincente
Un cambiamento che vale un risparmio energetico del 30%
Il passaggio da azionamenti in cc a quelli in ca elimina I problemi di manutenzione di un’azienda di packaging
Drives power slitter machines
Control Techniques at the heart of highly rated slitter machines
Prestazioni Incrementate Del 30%
Prestazioni di packaging migliorate del 30%
Processo
Simplified system design
Commander C laundry drive improves washes while reduces energy and water consumption
Gomma e plastica
9 million tyres get new lease of life
Business performance improvements for global retread company
Palco e intrattenimento
Unidrive, il protagonista della cerimonia di apertura dei Giochi Asiatici.
Nel 2023, oltre 12.000 atleti provenienti da 45 paesi si sono riuniti a Hangzhou, in Cina, per competere nella 19ª edizione dei Giochi Asiatici.
Il sogno del turista di un giorno
Dopo 200.000 viaggi, la funicolare vecchia di 30 anni viene ristrutturata
Fan power keeps dutch skydivers flying high
Drives produce 2.4MW of power to generate wind speeds up to 250km/h
La tecnologia che emoziona. Un’esperienza sensoriale ad alto impatto dal palco alpubblico
Star della musica mondiale si fidano ciecamente di innovative motion technology
Banchi di prova
La tecnologia avanzata al servizio dell’innovazione del futuro
Gli azionamenti ca a velocità variabile di controltechniques supportano l’innovazione dei costruttori di banchi dinamometrici
Pensare in grande per testare grandi motori
Maggiore capacità nell’impianto di prova motori
Textiles
Dalla seta al metallo
Soluzioni di motion integrate per telai speciali
Acqua
Aiutare La Natura
Azionamenti Commander C200 risparmiano energia e aiutano la natura
Approvvigionamento idrico garantito ed efficiente
Azionamenti Commander C200 utilizzo di risorse naturali per fornire alimentazione elettrica e controllare la gestione dell’acqua in aree che ne hanno maggior bisogno
Il controllo intelligente riduce il consumo di energia
Con Unidrive, la Fontana dei delfini di Singapore continua a regalare emozioni