Health monitoring or condition monitoring has been used for many years on machines and plant where the cost of an outage is high. It can allow failures to be anticipated and maintenance or repairs to be scheduled for the least loss of production, as well as avoiding unnecessary periodic maintenance.
It can be as simple as a person touring the plant at regular intervals with portable instruments such as a thermal imaging camera and vibration analyser, or it might be permanently installed so that data can be gathered remotely over a long period, the data analysed off-line and trends identified.
With the increasing use of intelligent devices on machinery and plant, which can be networked and their data gathered remotely at low cost, the possibility for plant health monitoring is increasing rapidly. There is plenty of information available on the web giving ideas and offering products for monitoring.
In this blog post, I will be pointing to a range of techniques which take advantage of the special position of the variable speed drive in the machine in order to access further useful data.
Machine safety on the shop floor
Generally speaking the techniques applied need to use low-cost sensors and to be reasonably non-invasive, so as to avoid high installation costs and the risk of damage from the installation process. Simple sensors such as thermal probes and accelerometers can be attached to accessible parts and give a wealth of data.
For example, an accelerometer can often easily be mounted on a bearing support or machine housing to measure radial vibration from a rotating machine, and it can detect defects which cause unbalanced forces, such as broken rotating parts, cracked shafts and misaligned couplings.
A simple amplitude measurement can give general warning of potentially damaging defects, whilst a deeper frequency analysis may be able to focus attention on particular parts especially if there are different rotational speeds involved as in gearbox or belt drives.
Machine or plant health monitoring using a variable speed drive
The variable speed drive is in a unique position in a machine since it usually provides the motive power. It is an intelligent device which is closely coupled to the working parts of a machine through the electric motor. It contains information which it uses to do its job reliably, but which can be accessed and analysed at little or no cost. In other words, it can be used as an extra set of sensors, at virtually no cost.
To begin with, the drive has its own internal sensors for various internal temperatures and the motor current, which are provided by the manufacturer to prevent damage to the drive or motor due to abnormal conditions. It may also have a motor temperature sensor connected. This data is available as drive parameters and can be accessed periodically to give a warning if it is approaching a limit, and to analyse trends.
In a closed-loop control system such as a servo drive, the drive contains data regarding the control variables. It is quite common for example to monitor the following error in a position control loop and to raise a flag if the error exceeds a threshold – this could indicate some kind of malfunction such as increased stiffness (impending seizure, obstruction or damage) or backlash (from wear).
It is a small step to move from a simple alarm threshold to monitoring the trend of the smoothed data and alerting the user to a developing situation which might result in future failure.
For following error there has to be at least a shaft transducer fitted, which tends to be the case in precision motion control applications. In all applications, however, the drive also has access to a special measurement which is difficult to obtain by external instrumentation – the motor torque.
Measuring motor torque
To measure motor torque conventionally using a transducer is most commonly done by installing a strain gauge or load cell in the fixing of the motor housing. This requires a special motor mounting if it is to give a sensible measurement of torque, and the measurement is affected by the moment of inertia of the heavy motor frame which reduces the sensitivity to the higher frequencies.
Even more difficult is to measure the actual dynamic shaft torque, since this requires a rotating strain gauge to be fixed to the shaft, with telemetry to pass the data to the fixed side. This is an expensive operation, and is done rarely even for a special test. It is unlikely to be a permanent installation.
The drive however has internal data for the torque-producing current in the motor, which is a good proxy for the shaft torque, available at no cost! The data is even available when the motor itself is inaccessible, whether deep inside a machine or under water or in a hazardous area. The accuracy of the torque measurement is best in a fully closed-loop system, but even in a simple open-loop drive the torque data is good enough for many purposes except at the lowest speeds.
Once we appreciate that torque data is available in the drive at virtually no cost, as well as the corresponding speed data, we can enter a new realm for machine and plant monitoring. The following is a range of possibilities which we have encountered at Control Techniques.
Readers may have new ideas for particular types of machines – it takes a detailed knowledge of the machine to invent new methods for using the torque data which is released by the drive.
The following list shows the information which the drive has, or could have at modest cost, all of which can be monitored and correlated to generate useful information about the machine:
Simple limits for average or peak torque
The real-time torque data can be smoothed to give a running average value when the drive is active, or the peak value can be captured on a timescale chosen to suit the application, this could be anything from milliseconds to days depending on the process. An alarm can be generated if the value moves outside of an expected range (i.e. it exceeds an expected value or, less commonly, falls below an expected value).
Trends of torque
The same torque data can be logged and analysed for trend over time or against any other variable, with alarms set to indicate an unhealthy trend.
Simple correlations of average torque with speed
In many processes the torque is strongly dependent on the speed, in a well-defined pattern. For example, a fan or pump driving fluid through a fixed duct, pipe or loop, or a network of them, will have a well-defined torque/speed curve. Any significant deviation from the normal curve indicates a change which might represent a problem. Some examples are:
Low torque:
- Broken drive belt or other coupling
- Loss of fluid in pump
- Obstruction to flow, e.g. blocked filter or screen (for an impeller type of pump or fan, could apply also to conveyor etc.)
- Buildup of deposits on fan or pump rotor
- Cavitation in a pump due to air ingress, swirl or other faults (also causes pulsations – see below)
High torque:
- Seizure of rotor or other parts (partial or total)
- Obstruction to flow (positive displacement type of pump)
- Major leakage (impeller type of pump or fan)
A torque/speed profile can be established outside of which an alarm state is generated, for example as shown in Figure 1.
The torque data needs to be subject to sufficient low-pass filtering or averaging to prevent dynamic effects (acceleration torque) or normal pulsations from generating false alarms.
Other variables may have an impact, for example, a variable delivery pressure of a fluid, so tolerance bands must be set wide enough to prevent false alarms from this cause.
Multi-variable correlations
In more complex processes the torque will depend on several variables, which might or might not be available to the drive. For example, consider a fan driving air through a system of ducts, some of which have damper controls to vary the local air flow. The torque/speed curve then depends on the positions of the dampers.
If data is available regarding the damper state, or the pressure drop over the dampers, then a multi-variable correlation may be possible to allow for this. Figure 2 gives a simple illustration of the case with two duct branches with dampers.
Another possibility is to use the measured torque and speed values to deduce the flow and pressure at the pump or fan from their characteristic curves, which could then be compared with a measured value from a transducer. Any discrepancy could mean either that the pump or fan is defective or the transducer is defective.
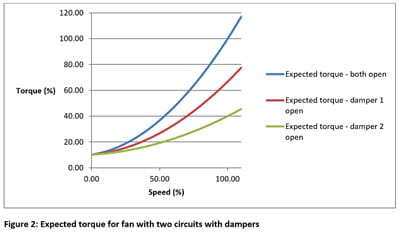
Dynamic analysis of torque
The torque data in the drive has a wide bandwidth and can in principle be used for dynamic analysis. It is quite common for the torque bandwidth to be in the order of 1 kHz or more, although it might not be possible to access and analyse the data at such a high rate – the data communications channel typically limits the data access to about a 250 ms sample interval.
The torque data relates to the electrical torque in the motor, which is transmitted to the output shaft but influenced by the inertia of the motor rotor and the effective stiffness of the motor control algorithm. These form a low-pass filter whose characteristics might not be known.
In a fully closed-loop system it is possible to deduce the transfer function and obtain accurate shaft torque data, so that for example high-frequency torque reversals can be detected. However the measurement does not need to be precisely calibrated in order for comparisons or trend analysis to be successful.
In practice pulsations with frequencies in the region of 100 – 500 Hz have been usefully monitored from motor electrical torque data.
Blocks of data can be captured in real time and subjected to dynamic analysis off line. Analysis may be in the time domain, for example by calculating the magnitude of fluctuations (overall torque pulsation or fluctuation, r.m.s. amplitude with or without time-averaging, peak values or peak negative values) or in the frequency domain through a Fourier transform with respect to time or some other variable such as position. This can then allow developing changes to be detected, specifically in the pattern of torque pulsation:
- Excessive torsional overall vibration amplitude, wide-band or band-limited, e.g. from broken machine parts or cavitation in pumps
- Excessive peak torques which might result in mechanical damage or premature wearout
- Frequent torque reversals which can cause gear chatter resulting in premature wear or breakage
- Torsional resonances, e.g. from loose couplings, resulting in peaks in the frequency spectrum whose frequency is independent of speed although they may be enhanced at certain speeds
- Torsional pulsations, with one or more cycles per revolution, e.g. from cracked shaft, impeller or gear tooth damage or other mechanical damage, with the possibility of tracing the source in a complex machine from the frequency of the spectral peaks, the speed, and a knowledge of gearbox or other drive ratios.
Dynamic analysis of torque with speed correlation
In some of the examples given above it is clearly beneficial to consider the shaft speed in conjunction with the dynamic analysis of torque, because pulsations relating to the rotation of the shaft will be at the rotational frequency (once-per-revolution effects) or a multiple of it (e.g. a cracked shaft gives twice-per-revolution, impellers may be at N-per-revolution, gear teeth at N or N1/N2 –per-revolution).
It can be helpful to generate compound plots of vibration spectral analysis with speed, which will clearly differentiate N-per-revolution effects from resonance effects whose frequency is fixed but might be stimulated only in certain speed ranges. These are referred to as cascade plots or waterfall plots, and are widely offered by suppliers of vibration analysis equipment.
Caution – sampling rates and aliasing
Care is needed in systems with rapid torque pulsations. The torque data is sampled at a rate which might be restricted by the capability of the drive to store or export data at the rate it is acquired internally. The sampling frequency will produce alias errors at frequencies such as (fs – fd) where fd is the frequency content of the data and fs is the sampling frequency. fs needs to be kept above about 3 times fd to avoid generating confusing new frequency products within the region of interest.
An added benefit of cascade plots is that alias products are clearly visible, their frequency falling as the speed increases whereas with genuine effects the frequency increases or remains constant.
Artificial intelligence analysis
In all of the above, I have concentrated on applications where a physical understanding of the process is used to define an expected behaviour, and the available data is used to compare actual operation with the expectation. Even if the amplitude scaling is uncertain, the frequencies are unique and trends can be identified.
The advantage of this approach is that people involved in the process can understand the data and work from the information and alarm conditions generated to develop a diagnosis for the plant.
An alternative is to use some form of machine learning algorithm to track all of the available data and aim to deduce the patterns of normal and abnormal behaviour. This is a subject of current research, for example https://phys.org/news/2016-02-scientist-ai-algorithm-machinery-health.html .
In conclusion
The ideas given above are general ones based on a broad picture of a machine with rotating parts, couplings and gears, or a pump or a fan. I hope that by pointing out the special access which the drive gives to some valuable data, especially the dynamic torque data, designers of machines will be able to apply these ideas to their own specific and unique applications.