The process that transforms a recently felled tree into a banded and wrapped stack of identical wooden planks is a dovetailed arrangement of mechanised and almost entirely automated events. Give or take the odd crane operator, forklift truck driver or control room figure, the whole story can be completed more or less without human involvement.
Conveyor belts and chains are the arteries of the system. They move the timber through the many phases of the operation: from the initial sorting area, through debarking, into the milling and sawing machines, through further sorting stages, into the kilns, and finally off to be planed and trimmed. More conveyors move sawdust and woodchips away.
From the force of water …
For the great motive power they require, sawmills throughout history have drawn on the energy resources of their day. In ancient and medieval times the force of water was harnessed; the industrial revolution brought steam power and greater mechanisation. Today’s sawmills make auxiliary use of natural gas, wood waste and fuel oil, though it is electrical energy that powers the signature machinery, from the debarkers and saws to the trimmers, edgers and planers, as well as all pumps and fans.
A sawmill’s energy consumption can represent up to 10% of its operating costs. Reducing this figure – even while increasing the number of cubic meters of timber cut – is fundamental to a healthy outlook for the industry.
… to the power of the AC drives
Much can be achieved through the upgrading of old, inefficient motors, a more appropriate loading of motors, and a reorganisation of the system’s variable speed drives. Easy-to-fit, wall-mounted, general-purpose AC drives can significantly enhance the precision and efficiency of the machines that control every maneuver from the feeding of logs into the head saw to the metering of the saw-line angle.
The greater the degree of automated process in the sawmill, the greater the importance of energy-efficient motors and drives. A two-saw edger, for example, deployed to straighten and smooth the sides of beams emerging from the head saw, is automated by replacing the handwheel formerly used to adjust the position of the saws with one or more motors. Drive-control is then responsible – to the millimeter – for the positioning of the edging blades.
Variable speed drives in sawmill machinery
The appropriateness of variable speed drives to sawmill machinery derives in part from the nature of the raw material. The different sizes and dimensions of the pieces being conveyed call for varying conveyor speeds and feed rates. If a load signal from the main drive controlling a saw is sent to and acted on by the drive that controls the conveyor feeding the wood into the saw, an adjusted feed rate and a constant load on the saw may be achieved. Performance is improved at the same time as energy use is optimised.
The kind of energy system available through the installation of AC drive power modules interconnected over a common DC bus will further bring down total kilowatt consumption by regenerating braking energy to the AC mains and circulating power between drives.
The ability to stop and start motors quickly not only increases productivity by cutting down on transition times. When it comes to milling machinery, the safety benefits of upgraded braking are obvious, especially where saws are located close to access doors. Replacing a simple DC injection braking system with one controlled by a configuration of AC drives can see emergency shutdowns – activated when an opened door sends a signal to the PLC – effected in a couple of seconds, even with mill heads rotating at up to 3,000 rpm and with high inertia.
Sawmill automation and safety
With greater automation, though, also comes a greater need for preventative maintenance. The domino-effect of localised mechanical breakdown in sawmills is far-reaching, potentially telegraphing right the way down the line. Drives are accordingly programmed to monitor such motor activity as kilowatt hours used (and saved) and cooling fan runtime, thus helping operations to function within safe limits. Retro-fitting an older sawmill with drives of this type represents a significant step towards improved performance, reduced energy consumption and lower operating costs. The number of parameters that requires setting on each drive is manageable and the screen interfaces are typically intuitive and user-friendly through set-up, use and diagnostics.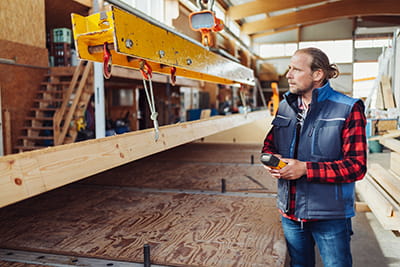
It goes without saying that the drives and PLCs used to operate a mill’s equipment should be appropriately ruggedized. Beyond this, the physical layout of the equipment in the back part of a sawmill should aim to direct the passage of worked-on timber over empty spaces through which dust and debris can freely fall onto the conveyor belts necessary for their removal.
For the largest sawmills, investment opportunities in new technology-applications continue to promise ever-more intelligent sorting, sawing and conveying of timber – from CT scanning to realise an internal picture of wood for optimal cutting, to software designed to assist in assigning commercial values to particular timber supplies.
Across mills of all sizes, however, and whatever the degree of automation, the key principle is that of connectedness within the big picture. On one level this may be the arrangement of drives so that energy shared along a bus relieves the need for superfluous braking resistors. On another, it could be the use of digital sensors and signals to flag up emerging issues before they cause expensive downtime.
The most efficient modern sawmill functions as a single, coherent organism. In this respect automation, as much as it represents the sum of its individual, programmable pieces of equipment, is ultimately a way of thinking about intelligent design.