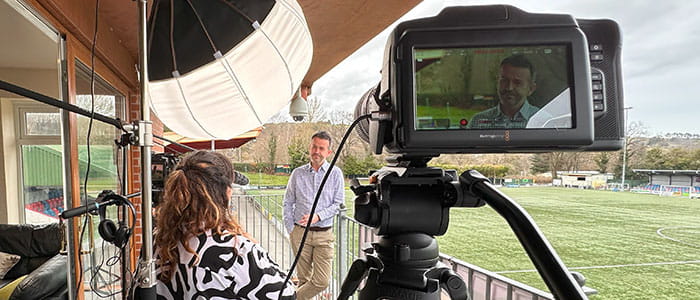
-
04 lipca 2025"The best drive is only as good as the support behind it" Industrial Automation India explore how Nidec Drives is delivering performance, intelligence, and sustainability to India’s fast-evolving industrial landscape.
-
25 kwietnia 2025W uznaniu ostatnich prac nad ujednoliceniem marek składowych i harmonizacją w ramach odświeżonej identyfikacji wizualnej Nidec, magazyn Transform przyznał firmie Nidec zarówno Złotą, jak i Diamentową Nagrodę za Najlepszą Architekturę Marki podczas Transform Awards Europe.
-
03 kwietnia 2025Nidec Drives ma przyjemność ogłosić nominację Laurenta Babaud na stanowisko prezesa.
-
26 marca 2025TOMRA, światowy lider w dziedzinie technologii recyklingu, stanęła przed wyzwaniem, gdy Holandia rozszerzyła swój system kaucyjny o puszki.
-
04 listopada 2024Wprowadzamy przełomową zmianę w naszym programie gwarancyjnym. Ze skutkiem natychmiastowym klienci otrzymają 5-letnią gwarancję w standardzie na wszystkie napędy, moduły opcjonalne i panele Nidec Drives.
-
23 października 2024
-
09 października 2024
-
28 sierpnia 2024Z rozbudowanego katalogu Control Techniques firma Trinca postanowiła wybrać serwosilniki Unimotor HD o wysokiej dynamice oraz serwosterowniki Digitax o wysokich parametrach, pracujące pod nadzorem kontrolerów ruchu MCe i MCz.
-
06 sierpnia 2024
Delve into the cutting-edge world of HVAC efficiency through the lens of permanent magnet motors.
-
09 lipca 2024Napędy Control Techniques Commander S wpisują się w dążenie firmy Nidec Drives do stałego rozwoju i są obecnie standardowo wyposażane w instalowaną fabrycznie osłonę zacisków.
-
06 czerwca 2024Płynna integracja i maksymalny komfort przy projektowaniu rozwiązań automatyki budynkowej
-
31 maja 2024The Secretary of State for Wales and Conservative candidate for Monmouthshire, David TC Davies, and Craig Williams, Conservative candidate for Montgomeryshire, have today (30th May 2024) visited the Nidec Drives UK Manufacturing Site, based in Newtown, Powys.