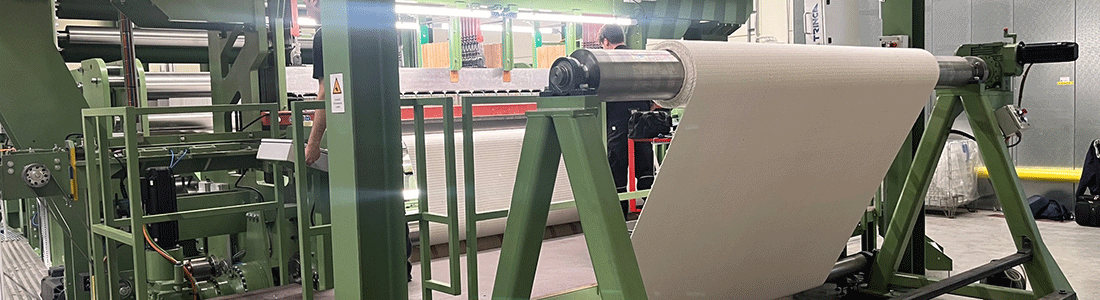
Integrated motion solutions for special looms
With Control Techniques’ integrated solutions, Trinca Technology manufactures some of the world’s most advanced looms, guaranteeing exceptional productivity and top quality even in the toughest applications.
The Italian textile machine industry is a global benchmark for technology and quality. Trinca Technology is one of the very few companies in the world today producing fully digital controlled looms with exceptional performance. With its operations in the province of Como, Trinca have moved from conventional cotton and silk to technical materials, particularly metal fabrics used for applications that include the production of packaging materials, geotextiles, meshes, kevlar and fabrics for other industrial uses.
Trinca have been innovators in textile machinery as electronics revolutionised the industry. Working in partnership with Control Techniques since the late 1980s they have utilised servo and automation technology to achieve greater precision and speed and eradicate mechanical changeovers.
The challenge
Most recently, Trinca’s goal was to develop an open, high-performing, fully digital platform that could produce their highest levels of output and quality while being easy to reconfigure for flexible production. Initially they decided to set up an in-house department for building operator panels and developing the related software, however, it was not long before they realised that it was too complicated to produce all components alone.
The solution
From the extensive catalogue of Control Techniques solutions, Trinca took advantage of the high-dynamic Unimotor HD servo motors and high-performance Digitax servo drives, controlled by MCe and MCz motion controllers.
The benefits
Trinca’s know-how is complemented by the performance offered by Control Techniques systems. Their latest generation looming machines are easy to configure and produce record performance levels, with gripper speeds up to 15 m/s, beating frequencies up to 250 bpm at a power equivalent of 80 tonnes.
Read the full case study:
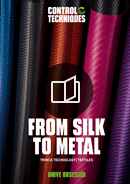