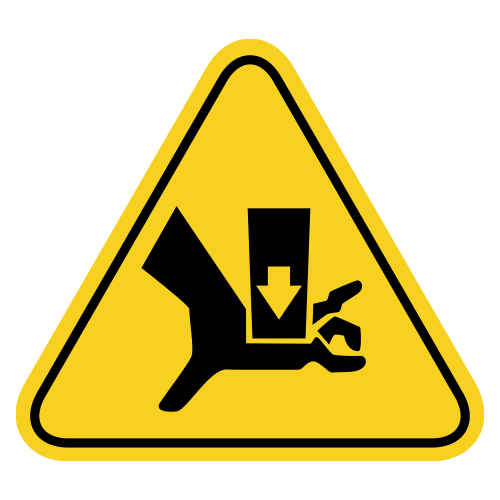
- Overview
- Specifications
- Downloads
What is functional safety?
Functional Safety entails the detection of a potentially dangerous condition resulting in the activation of a protective or corrective device or mechanism to prevent hazardous events arising or providing mitigation to reduce the consequence of the hazardous event.
In the design of a machine, a risk assessment must be performed and then updated regularly. As far as possible, the machine should be designed to be inherently safe, so that hazards are eliminated from the basic design. However, in most cases some risks remain at an unacceptable level and must be actively reduced using suitable control measures.
Why integrated safety?
The integration of motion safety functions in the drive supports a decentralized approach to the machine's functional safety that brings many benefits
- Reduced complexity and therefore design time
- Reduced wiring and consequential costs
- Ease of commissioning
- Speed of actuation due to close-coupling of safety function and drive
Benefits
![]() |
The conventional approach to functional safety relies on an external safety controller, electromechanical components to disconnect the drive from the motor and often additional sensors to monitor speed or position.
Integrated safety can dramatically reduce the cost and design time.
Onboard STO safely switches off torque to the motor negating the need for external contactors.
The addition of an MiS210 or MiS250 Safety option enables complex safe motion monitoring directly on the drive using the existing motor encoder.
While many applications can be completely solved with a drive-based distributed architecture, when an external safety PLC is required, drive integration is easily achieved using network safety protocols.
![]() |
When protecting people and equipment from hazards, timeliness is of the essence.
Integrated safety offers faster reaction times, thanks to the close-coupling of safety function and drive.
Support of the SafeEnDat protocol enables the use of functional safety certified encoders, with the ability to reach SIL 3 / PLe with a single motor-mounted encoder.
All of our integrated safety functions are externally certified to control category SIL 3 or PLe (Performance Level e).
![]() |
With an integrated safety solution from Control Techniques you always enjoy maximum flexibility, be it in the functional design or the choice of components and protocols to integrate.
The MiS210 and MiS250 options support several encoder protocols on up to 4 different channels wired to the drive or directly to the module. Onboard Motion Safety Functions support multiple instances and safe logicblocks are also available to allow implementation of complex safety chains.
Control and monitoring of the functions, as well as transfer of safe position and speed values are available over the main safety fieldbuses: CIP Safety over EtherNet/IP and FSoE over EtherCAT
Reduce downtime with motion safety
When human intervention is required to carry out inspection and repair or simply during production, it is essential to protect personnel from interaction with dangerous moving parts.
A comprehensive selection of Motion Safety Functions offers the flexibility to provide maximum protection whilst minimizing the impact on machine availability.
Brake and stop |
|
![]() |
Safe Torque Off (STO) prevents the drive from generating toque in the motor. The drive’s DC link stays energized, allowing for a fast restart |
![]() |
Safe Brake Control (SBC) can be used in conjunction with STO for the safe control of an electromechanical brake |
![]() |
Safe Operating Stop (SOS) keeps the energized motor in a safely monitored standstill condition |
![]() |
Safe Stop 1 (SS1) allows a controlled stop of the motor before removing power via the Safe Torque Off |
![]() |
Safe Stop 2 (SS2) allows a controlled stop of the motor followed by a Safe Operating Stop condition |
Speed and acceleration monitoring |
|
![]() |
Safely Limited Speed (SLS) safely monitors the motor speed to keep it within a specified limit |
![]() |
Safe Speed Monitor (SSM) provides a safe signal to indicate the motor is operating below a specified speed limit |
![]() |
Safely Limited Acceleration (SLA) safely monitors the motor acceleration to keep it within a specified limit |
![]() |
Safe Direction (SDI) safely monitors the motion direction |
Position monitoring |
|
![]() |
Safely Limited Position (SLP) monitors the absolute position of the motor to prevent it from moving outside of the specified range |
Network safety |
|
![]() |
Safe Value Transfer safe position and speed value transfer over safety fieldbus for further processing by safety controller |
Additional functions |
|
![]() |
STHC3 – Safe Two-Handed Control safely monitors the contemporary application of two push-buttons |
![]() |
Safe Emergency Stop (SES) safe monitoring of an emergency stop button |
Network Safety
More safety with less wiring
Activate and monitor all motion safety functions over the fieldbus for minimum wiring and maximum flexibility.
The black channel principle allows safety data to travel alongside standard, non-safety-relevant information on the same Ethernet medium.
This means that even complex safety configurations can be implemented with minimal wiring and without changes to the existing network topology.
MiS210 and MiS250 safety options support all the main industry standards for easy integration in any automation architecture.
- CIP-Safety on EtherNet/IP
- Safety over EtherCAT (FSoE)
For extra flexibility, safe position and speed values can be transferred to an external controller for further processing.
Support for the Safe EnDat protocol means that the maximum safety integrity level can be achieved without the need for extra wiring and additional feedback devices.
Configuring Safety
![]() Connect is our latest drive configuration tool for commissioning, optimising and monitoring drive/system performance. Download |
|
![]() SISTEMA is the most popular tool for the calculation of the safety performance level in the context of ISO 13849-1. It is available free of charge on the DGUV website. All safety-related parameters of our products are conveniently available as a SISTEMA library for easy integration. Download |
All Unidrive and Digitax drives offer onboard STO as standard.
The MiS210 and MiS250 safety option modules extend the built-in STO with the ability to safely monitor and/or restrict the scope of motion.
Safety Option Module | Unidrive M700 | Digitax HD | |
![]() |
![]() |
![]() |
|
|
|||
Order No. 82400000021100 |
Order No. 82700000021500 |
||
Safe I/O |
STO Integration | "blade" connector | wired |
Safe Input Pairs | 4 | 4 | |
Safe Outputs | 2 | 1(+1 used for STO) |
|
Pulse Outputs | 2 | 2 | |
Encoders |
Local Encoders |
2 | 2 |
Encoder PSU | 1 | 1 | |
Encoder external PSU Monitoring |
1 | 1 | |
Network Safety | Safety over EtherCAT (FSoE) |
with SI-EtherCAT |
on M753 |
CIP Safety |
on M700/M702 |
on M750 |
|
Motion Safety Functions (instances) |
Safe Stop 1 |
1 | 1 |
Safe Stop 2 |
1 | 1 | |
Safe Operating Stop |
4 | 4 | |
Safe Brake Control |
1 | 1 | |
Safely Limited Speed |
4 | 4 | |
Safe Speed Monitor |
4 | 4 | |
Safely Limited Acceleration |
4 | 4 | |
Safe Direction |
2 | 2 | |
Safely Limited Position |
4 | 4 | |
Safe Datum |
1 | 1 | |
Safe Value Transfer |
Position, Speed |
Position, Speed |
|
Safe Two-Handed Control |
1 | 1 | |
Safe Emergency Stop |
1 | 1 |