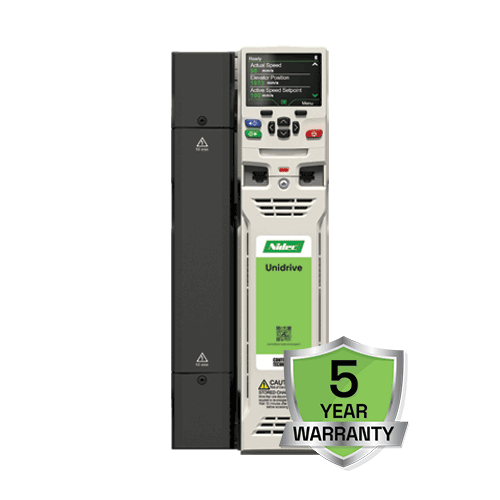
1.0 - 4,200 hp (0.75 kW – 2.8 MW) Normal Duty
1.5 hp – 4,200 hp (1.0 kW – 2.8 MW) Heavy Duty
208 - 240 V | 380 - 480 V
- Overview
- Specifications
- Options
- Downloads
Control Techniques’ Unidrive HS70 series high-speed variable frequency AC/Servo drives deliver enhanced control of high speed motors. Additionally, machine throughput is maximized through enhanced single axis control and multi-axis network synchronization. Onboard real-time Ethernet (IEEE 1588 V2), onboard Advanced Motion Controller, and high speed I/O for position capture enables machine builders to create more sophisticated and flexible machines.
The onboard Ethernet is also compatible with EtherNet/IP, Modbus TCP, and Real-Time Motion over Ethernet (RTMoE) for network flexibility.
To meet the needs of any application Unidrive M700 series is available in three variants:
- Unidrive HS70: Onboard Ethernet and single STO input
- Unidrive HS71: Onboard RS485 to upgrade from Unidrive SP, single STO input
- Unidrive HS72: Onboard Ethernet, dual STO inputs
Features
Maximize throughput with superior motor control
- High bandwidth motor control algorithm for open and closed loop induction, synchronous permanent magnet, and servo motors with up to 3,000 Hz current-loop bandwidth and 250 Hz speed loop bandwidth for smooth, efficient motor control
- Flexible speed and position feedback interface supports a wide range of feedback technologies from robust resolvers to high resolution encoders
Optimize system performance with onboard Advanced Motor Controller
- Unidrive HS70 series incorporates an Advanced Motion Controller capable of controlling 1.5 axes. The motion functions are carried out 'on the drive' so that system performance is maximized
Design flexible centralized and decentralized control systems
- MCi modules can be added to execute larger programs for advanced system control capability and can operate as network control masters
- Onboard PLC for logic programs reduce or eliminate the need for external controllers
- Machine Control Studiois an industry standard IEC61131-3 programming environment for efficient system design and configuration used to program the onboard PLC and the co-processor MCi module
- Complete IEC 61131-3 programming environment Structured text (ST), function block (FBD), sequential function chart (SFC), ladder diagram (LD), instruction list (IL), and continuous function chart (CFC)
- Three System Integration module slots are available to fit additional fieldbus, Ethernet, position feedback, machine control, and expanded I/O options.
Unidrive HS70 and Unidrive HS72 onboard communications
- Integrated dual port Ethernet switch provides simple connectivity using standard connections
- Onboard real-time Ethernet (IEEE 1588 V2) uses RTMoE (Real Time Motion over Ethernet) to provide fast communication and accurate axis synchronization
- Onboard Ethernet supports EtherNet/IP and Modbus TCP communications
Unidrive HS71 onboard communications
- Integrated dual port RS485 provides Modbus RTU connectivity using standard connections
Conform to safety standards, maximize uptime and reduce costs by integrating directly with safety systems
- Unidrive HS70 and Unidrive HS71 has an integrated Safe Torque Off (STO) input and can accommodate an SI-Safety module for safe motion functions; Unidrive HS72 variant has dual Safe Torque Off (2x STO)
Software
![]() Connect is our latest drive configuration tool for commissioning, optimising and monitoring drive/system performance. Learn More |
|
![]() Control Techniques' Machine Control Studio provides a flexible and intuitive environment for programming new automation and motion control features. Learn More |
This product comes with 5-year warranty as standard
No registration. No extra cost. Just peace of mind from day one. Learn more.
Key data
Single drive Heavy Duty ratings:
- 230 V: 1.0 hp to 50 hp (0.75 kW to 37 kW)
- 460 V: 1.0 hp to 125 hp (0.75 kW to 75 kW)
Single drive Normal Duty ratings:
- 230 V: 1.5 hp to 60 hp (1.1 kW to 45 kW)
- 460 V: 1.0 hp to 150 hp (0.75 kW to 90 kW)
Modular drive ratings:
- 125 hp to 4,200 hp (1.0 kW to 2.8 MW)
Control connections: Variant dependent
- Unidrive HS70 and Unidrive HS71 models: 3 x Analog inputs, 3 x Digital inputs, 2 x Analog outputs, 3x Digital I/O, 1 STO, 1 x Relay
- Unidrive HS72 model: 3 x Digital inputs, 3 x Digital output, 2 x STO, 1 x Relay
Feedback: 2 x Encoder inputs, 1 x simulated encoder output
Intelligence: Onboard PLC and Advanced Motion Controller (AMC)
Onboard communications: Variant dependent
- Unidrive HS70 and Unidrive HS70 models: Ethernet (EtherNet/IP, Modbus TCP, RTMoE)
- Unidrive HS71 model: RS485 (Modbus RTU)
Machine Safety: Variant dependent, SIL3/PLe compliant
- Unidrive HS70 and Unidrive HS71 models: Single Safe Torque Off terminal
- Unidrive HS72 model: Dual Safe Torque Off terminals
Keypad: No keypad (standard)
- KI-KEYPAD-LCD: Plain-text, multi-language LCD keypad for in-depth parameter and data descriptions for enhanced user experience
- KI-KEYPAD-RTC: All the features of KI-Keypad-LCD, plus a battery operated real-time clock which allows accurate time stamping of events, aiding diagnostics
- REMOTE-KEYPAD: Remote mountable, plain-text, multi-language LCD keypad allows flexible mounting outside of a panel and meets IP66 (NEMA 4)
- REMOTE-KEYPAD-RTC: The keypad is remote mountable, enabling flexible mounting on the outside of a panel (meets IP54/ NEMA 12). Three line plain text, multi-language LCD keypad for rapid set-up and helpful diagnostics. Battery operated real-time clock allows accurate time stamping of events, aiding diagnostics.
System Integration options slots: 3
Parameter cloning: PC tools, SMARTCARD, and SD card
VOLTAGE RATING |
|
100 V (100 V - 120 V ± 10%) |
|
200 V (200 V - 240 V ± 10%) |
✓ |
400 V (380 V - 480 V ± 10%) |
✓ |
575 V (500 V - 575 V ± 10%) |
|
690 V (500 V - 690 V ± 10%) |
CONTROL MODE |
|
Open-loop vector or V/Hz induction motor control |
✓ |
Open-loop Rotor Flux Control for induction motors (RFC-A) |
✓ |
Open-loop permanent magnet motor control (RFC-S) |
✓ |
Closed-loop Rotor Flux Control for induction motors (RFC-A) |
✓ |
Closed-loop permanent magnet motor control (RFC-S) |
✓ |
Active Front End (AFE) power quality convertor |
✓ |
Approval & Listings
cUL |
USA and Canada (cUL Listed). UL File number: E171230 |
CE |
European Union (all applicable directives and regulations LVD, EMD, RoHS, REACH, Energy related products) |
UKCA |
United Kingdom (all applicable regulations) |
RCM |
Australia and New Zealand (Responsible Supplier Registration No. E6934) |
EAC |
Russian Customs Union. All Unidrive-M models |
Functional Safety |
Safe Torque Off function. TÜV Rheinland Type Examination Certificates (includes HS70, HS71 and HS72): 01/205/5270.02/17 (Unidrive-M and derivative products) 01/205/5409.02/21 (SI-Safety option module) 01/205/5720.00/19 (MiS210, MiS250 option modules) The safety function "Safe Torque Off" can be used in applications up to Cat 4. PL e according to EN ISO 13849-1, SIL 3 according to EN 61800-5-2/ EN 62061/ IEC 61508, and in lift applications according to EN 81-1 and EN81-2. |
UL Functional Safety |
Unidrive-M all products |
Functional Safety |
TÜV Nord certificates:44 799 17002402 (Frequency converters with Safe Torque Off function for lift drives) |
ISO |
Quality system: ISO 9001 (Certificate Nos. FM 739405) |
China RoHS |
Chinese Order No. 32, 2016; Administrative Measures for the Restriction of Hazardous Substances in Electrical and Electronic Equipment (China RoHS 2), |
EPA TSCA regulations |
All Commander and Unidrive-M products |
IHM, Basel convention, |
MEPC 68/21 / Add.1, Annex 17, Resolution MEPC.269(68) 2015 Guidelines for the development of the inventory of hazardous materials. |
Responsible Minerals Initiative (RMI) |
CMRT compliance |
Weights & Dimensions
SINGLE DRIVES:
FRAME SIZE |
DIMENSIONS (H X W X D) |
WEIGHT |
||
mm |
in |
kg |
lb |
|
3 |
382 x 83 x 200 | 15.0 x 3.3 x 7.9 | 4.5 Max | 9.9 Max |
4 |
391 x 124 x 200 | 15.4 x 4.9 x 7.9 | 6.5 | 14.3 |
5 |
391 x 143 x 200 |
15.4 x 5.6 x 7.6 |
7.4 |
16.3 |
6 |
391 x 210 x 227 | 15.4 x 8.3 x 8.9 | 14 | 30.9 |
7 |
557 x 270 x 280 | 21.9 x 10.6 x 11.0 | 28 | 61.7 |
8 |
803 x 310 x 290 | 31.6 x 12.2 x 11.4 | 52 | 114.6 |
All dimensions include mounting brackets
MODULAR DRIVES:
FRAME SIZE |
DIMENSIONS (H X W X D) |
WEIGHT |
||
mm |
in |
kg |
lb |
|
INVERTER & RECTIFIER | ||||
9A |
1108 x 310 x 290 | 43.62 x 12.21 x 11.4 | 66.5 | 146.6 |
9E | 9T |
1069 x 310 x 290 | 42.1 x 12.2 x 11.4 | 46 | 60 | 101.4 | 132.3 |
10E | 10T |
1069 x 310 x 290 |
42.1 x 12.2 x 11.4 |
46 | 60 |
101.4 | 132.3 |
11E | 11T |
1242x 310 x 312 | 48.9 x 12.2 x 12.3 | 63 | 65 | 138.9 | 143.3 |
INVERTER |
||||
9D |
773 x 310 x 290 | 30.4 x 12.2 x 11.4 | 34 | 75 |
10D |
773 x 310 x 290 | 30.4 x 12.2 x 11.4 | 34 | 75 |
11D |
863 x 310 x 312 | 34 x 12.2 x 12.3 | 42 | 92.6 |
RECTIFIER |
||||
10A |
6 pulse 355 x 310 x 290 |
6 pulse 15.8 x 12.2 x 11.4 |
12 | 26.5 |
11A | 11T |
6 pulse 415x310x290 12 pulse 415x310x290 |
6 pulse 16.3x12.2x11.4 12 pulse 16.3x12.2x11.4 |
21 | 23 | 46.3 | 50.7 |
All dimensions include mounting brackets