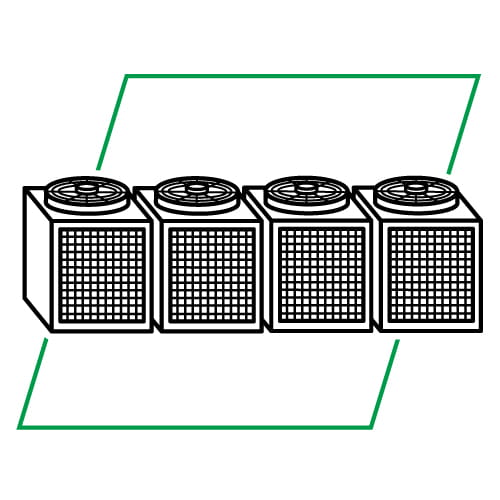
Duty Assist pump control
The Duty-Assist control is an effective method of controlling multiple pumps or fans in parallel, to maintain the required process demand.
This solution uses the Unidrive M with system control provided by an SI-Apps-Plus module (legacy solution) or a MCi210 module.
Duty Assist Features
Pumps and fans are often used in parallel banks to:
-
Avoid motor overload
-
Security of supply (system redundancy)
-
Reduce running cost due to system load cycles
-
Provide wide range of control and flexibility
Typically in a parallel bank of three it is usual to find two running and one standby. The system consists of a ‘Duty’ drive and assist starters. The assist starters can be of any type, (e.g. D.O.L, Star-Delta, Auto-Transformer, Soft Starter or Inverter); the choice is dependent on the system limits. The Duty drive can control one dedicated motor (‘Fixed Duty’), or with additional external switchgear could be selected to control other motors within the parallel configuration (‘Flexible Duty’).
The Duty is controlled by a PID loop which will maintain the process level required, if the demand exceeds the capacity that can be derived from the Duty, then an Assist starter will be enabled to assist with the delivery. If the demand continues to increase additional starters will be called upon.
When the demand decreases, then each assist starter will be deselected to reduce the delivery to the required demand.
All the system control is achieved by the add-on solution module. The I/O interfacing is provided by the standard I/O on the drive, and depending on the number of starters required, the additional SI-I/O module. These are both fitted within the drive SI option slots.
The Duty Assist Solutions software has the following functions:
- Fixed Duty Motor - up to 4 assist starters can be controlled.
- Flexible Duty Selection - up to 3 assist starters can be controlled.
- Assist or Duty selection can be by runtime or by a set sequence.
- Automatic reselection if the requested assist fails to start.
- Local/Remote, digital control selection from the Unidrive M700/701 terminal I/O or via fieldbus.
- Standalone or system configurable.
- Set points and feedbacks can be derived as direct analog signals or by fieldbus.
- Process high and low trip thresholds, (selectable).
- Inverse speed characteristic, (selectable).
- No Flow protection, (selectable).
- Wake/Sleep, energy save function, (selectable).
- Dynamic V/F, energy save function, (selectable).
- Cascade System Stop, (selectable).
- Two selectable preset process set points for day/night control with external clock.
- Auto-changeover to ensure starters are not continually running for long periods of time, (selectable).
- Assists number of starts per hour protection, (selectable).
- Assist Override to react to peak demands, (selectable).
- All data set up in real engineering units.
- Optional Fieldbus Interfaces: CTNet, Profibus-DP, DeviceNet, CANopen, Modbus RTU, Profinet-RT, Ethernet, EtherCAT.