Looking back over 50 years of Variable Speed Drives (VSDs) and the machines that transformed industrial automation.
The half century leading up to 2023 saw a technological revolution that is sometimes overlooked, yet it is a period when leading drive developers and manufacturers, were at the forefront of industrial innovation and change.
We’ll take a look at how drives fit into the broader history of industrial automation, and understand more about how that history has shaped the way we live.
Efficiency of mechanisation over man alone dates back centurie
Early humans started to sharpen stones as cutting tools over 2 million years ago in the Great Rift Valley of East Africa. Ever since we have depended on increasingly sophisticated tools and devices to perform tasks more efficiently and productively than people on their own can do. The modern story of industrial automation, or how we learnt to use machines in place of people to make things, begins with the Industrial Revolution in 18th Century Britain.
New inventions like the spinning jenny (which could automatically spin many spools of cotton or wool thread at the same time) and the power loom (a machine for weaving cloth) greatly increased the speed and efficiency of producing textiles; and the development of the steam engine provided a new source of power to replace human muscle.
Soon steam-powered machines were transforming manufacturing and other industries. They could operate continuously and produce goods faster than humans working by hand. This allowed for the mass production of goods in factories, leading to lower prices and increased accessibility for consumers.
Automated manufacturing set the trend for modern society
The new automated manufacturing processes spread across Europe and the United States throughout the 19th Century. Economic growth exploded, and the population increased. As people shifted from agricultural to industrial work, they moved from the countryside to towns and cities, extended families split up, and new ideas and identities took hold. For better or worse, modern society was taking shape.Automation took another leap forward with the widespread adoption of the assembly line in industrial manufacturing. The idea of moving a product along a line so each worker could specialise in a particular task and perform it again and again on a different unit was not new, but the introduction of mechanised conveyor belts in the late 19th Century increased the capabilities of the assembly line.
Assembly lines allowed for mass production of goods
Henry Ford started making the Model T Ford motor car at Highland Park Ford Plant in Michigan, USA using an assembly line in 1913. Cars came off the line every 3 minutes, each car needing only 1.5 labour-hours to produce, compared to the previous 12 labour-hours. The reduction in costs made complex manufactured goods like cars affordable to ordinary workers for the first time, even if the rigid processes of the assembly line meant that consumer choice was limited - Ford said your car could be any colour you wanted, as long as it was black!The assembly line allowed for the mass production of goods at a much faster rate than with traditional methods of manufacturing. It also led to the development of specialised machines and tools that could perform specific tasks in sequence.
Variable speed drives empowered the possibilities of the electric motor
The industrialisation of the 18th and 19th Centuries was powered by steam, but the advances of the 20th Century depended on the more efficient and controllable power of electricity. The British scientist Michael Faraday discovered the principle of generating electricity with a magnetic field in 1813, and the Serbian/US inventor Nikola Tesla was a leading contributor to the development of workable electric motors in the late 19th Century.Electricity had many advantages as a source of power; it was clean, efficient, easily transportable, powerful and could be switched on and off in an instant, unlike a horse or a steam engine. The development of electric motors greatly expanded the possibilities of industrial automation, powering machines that were more efficient and controlled than steam-powered ones.
However, the full potential of electric motors in automation could not start to be realised until the invention of the VSD in the 1950s. VSDs control the speed and torque (the available twisting force) of electric motors, which enables precise control of the movements of machinery and other automated systems, essential for complex processes and the handling of delicate materials.
Drives provided the missing link to automate more sophisticated processes through that precise control over the speed and torque of motors. They also enable significant energy savings by adjusting the speed of motors to provide the required load only when needed, and improve system reliability and extend the lifespan of equipment by reducing wear and tear on motors.
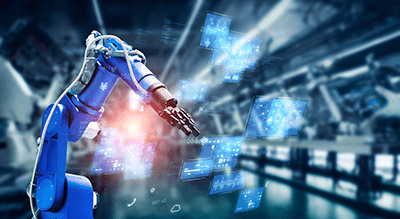
Drives became cheaper, more reliable, and more powerful
Early drives were bulky and unreliable but started to change when a series of smaller, cheaper, more reliable, more powerful and more intelligent drives were being introduced to the market to meet increasing demands from consumers. At this time the world’s first fully micro-processor controlled drive was developed and launched. The power, flexibility and control of the new drives transformed the capabilities of electric motors in industrial automation. The use of drives is now widespread, and almost any task, however complicated, can now be automated.Modern drives have advanced computing and communication capacity, allowing full integration into complex autonomous production systems using artificial intelligence (AI). AI algorithms are used to analyse data, make predictions and decide actions in real time, enabling machines to operate more independently and adapt easily to changing conditions. This helps to optimise production processes, improve quality control and reduce costs. AI is increasingly important in industrial production, and has taken automation to a new level. Indeed, some experts believe there is a genuine risk in the future of AI machines escaping human control and attempting to take over!
Another important development in the 1960s was the introduction of robots in manufacturing. Robots are now able to perform tasks with a high degree of precision and speed, and are an important part of many automated processes. They can operate continuously, increasing efficiency and productivity, and are particularly useful in situations that are dangerous for humans. Owners of household vacuum cleaner robots will know that they can also be handy for tackling dull and repetitive jobs!
Automation has influenced every aspect of our society
What does the future hold for industrial automation? The phrase Internet of Things (IoT) describes a network of smart devices with sensors and processing capabilities that can communicate with each other. Integrating AI and the IoT into industrial automation will mean that production systems can sense, analyse and make decisions for themselves, with drives providing the crucial connection between the digital brain and the physical muscle of the electric motor.
In 250 years we have come a very long way from the spinning jenny at the start of the Industrial Revolution. The power and scope of industrial automation has influenced every aspect of our society, and will continue to do so. Machines are now able to do almost anything humans can. But only we can decide if we use that power to make life better, or worse for ourselves and the rest of the planet.