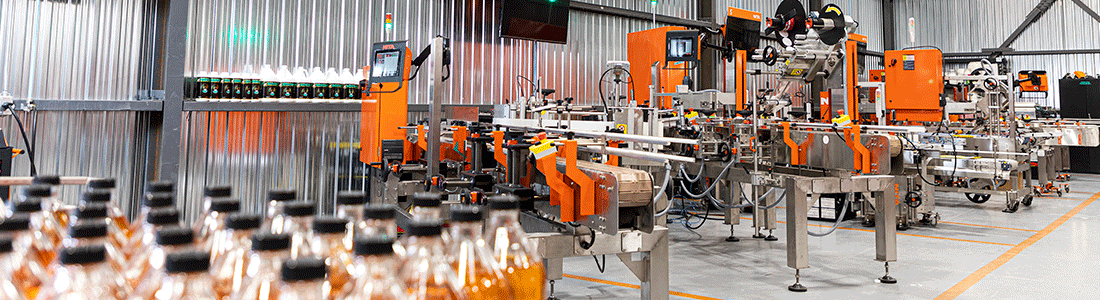
The challenge
Nita has consistently been at the forefront of offering unmatched innovation and technology and superior performance when it comes to inline labeling systems. Luc Harvey, Chief Engineer at NITA explains “We build the world’s most technologically advanced labeling systems right here in North America. Every NITA machine is designed to increase production efficiency, reduce operator headaches, eliminate downtime from unscheduled (or unplanned) maintenance and repairs, and generally make everyone’s lives easier! In today’s highly competitive, quickly evolving technological environment, innovation is essential and is the key to securing our growth.” Always on the lookout for ways to improve the performance of its machines, NITA turned to its trusted control partner Control Techniques, for an upgrade to its current solution.
The solution
The Control Techniques team recommended Digitax HD M754 MCI as a replacement to NITA’s earlier servo drive. Today M754 controls the modules on NITA’s Sentient Labeling Systems, including conveyor speeds, metering belts, orientation belts, and labeling heads.
The compact Digitax M754 has a powerful MCi second processor onboard which brings a whole host of machine design opportunities for the NITA engineering team. The onboard MCi processor executes comprehensive programs that seamlessly control multiple drives and motors simultaneously across real-time networks.
Furthermore, Onboard Ethernet using RTMoE (Real Time Motion over Ethernet) provides synchronization and communication between drives using the Precision Time Protocol (PTP) as defined by IEEE1588 V2.
The benefits
When developing its new Sentient Labeling Systems, the requirements were that the servo drives should be robust and small, while at the same time being powerful and highly efficient. “We particularly like the Digitax Servo drive series for its optimized servo performance and straightforward connectivity – it’s quick and intuitive to configure too.” said Luc Harvey, Chief Engineer. The servo drive upgrade provides NITA’s next generation of Sentient Labeling Systems with the following benefits:
- Maximised throughput with superior and precise motor control
- Seamless motor-drive pairing
- Unparalleled machine control scalability
- Flexible machine design with option modules
- Reduced commissioning time
- Increased machine safety
- Improved machine diagnostics
- High reliability in demanding 24x7 manufacturing environments
Compared to its predecessor, the M754 is much more compact, which helps reduce the space needed in control cabinets by up to 25%. Measuring only 40 mm (1.6”) wide, they can be mounted side-by-side, minimizing the footprint and allowing NITA to build the most compact control cabinet possible, resulting in reduced cost. Furthermore, the new drives feature easy-access quick connectors — The result is faster and easier electrical installation.
Moreover, the patented Ultraflow™ ventilation technology provides optimal heat dissipation by expelling the excess heat outside of the cabinet through the rear of the drives.
This helps reduce premature wear on all electrical components and allows NITA’s machines to operate at peak efficiency at all times. The servo motors are protected to an IP67 rating, ensuring prolonged performance in some of the most challenging environments.
This project is a great example of how it is possible to reduce manufacturing costs through innovative motion technology, while also significantly improving the overall machine productivity. This was achieved without having to change any of the existing machine mechanics, but rather by focusing on better servo drive control.
“As a Labeling Machine manufacturer, it is important for us that our systems are adaptable, scalable, intuitive, and connected. The combination of Control Techniques' servo drives and servo motors allows us to offer the latest in cutting edge labeling technology and to future-proof the design for our next generation of labeling systems. Innovation is critical to our company’s success in today’s highly competitive and high-speed market. Customers are more demanding and now rely more than ever on machine performance metrics to make data-driven decisions. Our goal is to provide customers with fully automated, state-of-the-art labeling solutions to maximize their manufacturing productivity and efficiency. Control Techniques deliver top-notch products and services to help NITA achieve this goal; they have been with us every step of the way.”
Chief Engineer at NITA
Read the full case study:
Impressed? Contact us for your automation needs