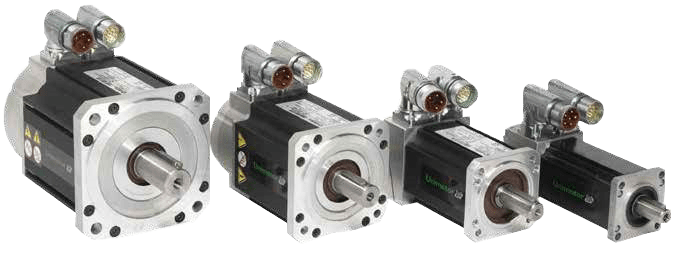
- Overview
Nidec, the leader in brushless DC motor technology, produces over 1 million brushless DC (BLDC) motors per day. BLDC motors are generating a lot of attention as they gain momentum within various industries. The advantages of BLDC motors have made them the premier choice for many OEMs, robotics companies and material handling specialists. As they don’t require brushes, there is less need for maintenance and one less point of failure, which helps make them more cost-effective than brushed motors.
Nidec produces well-developed BLDC motors that are efficient, robust and economical. Our engineering teams have worked on a wide variety of designs and applied their collective expertise to create Nidec's diverse portfolio of motors. Contact Us today for more information about our motor selection or to inquire about custom solutions to meet your specific requirements.