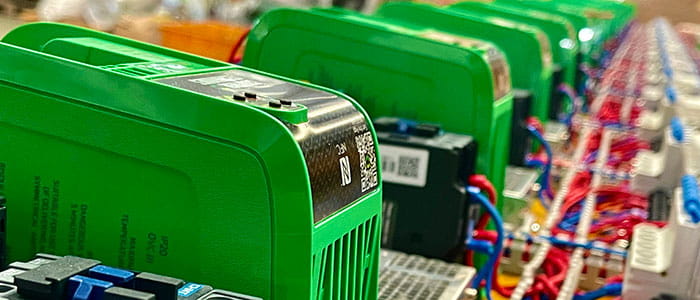
Żywność i napoje
Honey harvesting
Commander C ensures the delicate automatic operation of honey extraction
Drives power slitter machines
Control Techniques at the heart of highly rated slitter machines
30% wzrost wydajności pakowania
30% wzrost wydajności pakowania
HVACR
Commander stops noisy vibrations at bowling alley
Improved customer experience and energy savings
Pralnictwo
Szybka dostawa ratuje z opresji
Szybka dostawa ratuje producenta płyt sufitowych z opresji
Sterowanie Maszynami
Zwiększanie wydajności w Nidec Drives
studium przypadku w zakresie zaawansowanej automatyzacji produkcji
Transport materiałów
Rewolucja w redukcji odpadów opakowaniowych
Nidec Drives i gospodarka o obiegu zamkniętym
Przeładunek ładunków masowych pomaga utrzymać jakość produktów
Napędy Unidrive M400 I M701 napędy Control Techniques pozwalają uzyskać więcej ton przeładunku materiałów na metr kwadratowy niz w jakimkolwiek innym zakładzie
Innovative companies need innovative suppliers
Variable speed drives achieve weight accuracy of 0.025%
Compressor boosts performance
Efficient drives process 120,000 tonnes of waste per year
Metale
Serwosterowanie w próżni
Serwosterowanie w próżni
Pakowanie
Future-ready labeling technology
Digitax maximises throughput with precision motor control
Perfekcyjnie Pakowane
Napędy unidrive M700, Commander C300 I Digitax HD pracują wspólnie dla poprawy zarządzania przepływem powietrza oraz redukcją zużycia energii dla specjalistów od maszyn pakujących
Napędzamy sukces
Napędy Unidrive M700 partnerstwo z Control Techniques to potężny pakiet
30% oszczędności energii dzięki wymianie napędów
Dostawca opakowań pozbywa się problemów dzięki wymianie napędów dc na napędy ac
Napędy zasilające maszyny do cięcia wzdłużnego
Control Techniques bijącym sercem wysoko ocenianych maszyn do cięcia wzdłużnego
Digitax boosts performance by 30% at Italian food packaging plant
Improved throughput and quality
Proces
Simplified system design
Commander C laundry drive improves washes while reduces energy and water consumption
Guma i tworzywa sztuczne
9 million tyres get new lease of life
Business performance improvements for global retread company
Scena i rozrywka
Unidrive - gwiazda ceremonii otwarcia Igrzysk Azjatyckich
W 2023 roku ponad 12 000 sportowców z 45 krajów zgromadziło się w Hangzhou, w Chinach, aby rywalizować w 19.
Marzenie pełnoetatowego turysty
30-Letni napęd, po 200 000 cyklach pracy, doczekał się remontu
Fan power keeps dutch skydivers flying high
Drives produce 2.4MW of power to generate wind speeds up to 250km/h
Efekty sceniczne lift music productions
Światowe gwiazdy muzyki w pełni wierzą w innowacyjną technologię ruchu
Stanowiska testowe
Advanced technology meets cutting edge innovation
Control Techniques variable speed ac drives support innovation from dynamometer manufacturers
Duża pomysło wość w testowaniu dużych silników
Zwiększona wydajność stacji prób silników
Tekstylia
Od jedwabiu do metalu
Zintegrowane rozwiązania ruchowe dla krosien specjalnych
Woda
Odwdzięczamy się przyrodzie
Napędy Commander C200 oszczędzają energię I odwdzięczają się przyrodzie
Zapewnienie darmowej wody do winnicy
Napędy Commander C200 wykorzystanie zasobów naturalnych do zasilania I kontrolowania gospodarki wodnej w najbardziej potrzebujących obszarach
Inteligentne sterowanie oszczędza energię
W singapurskiej fontannie z delfinami woda płynie dzięki napędom Unidrive