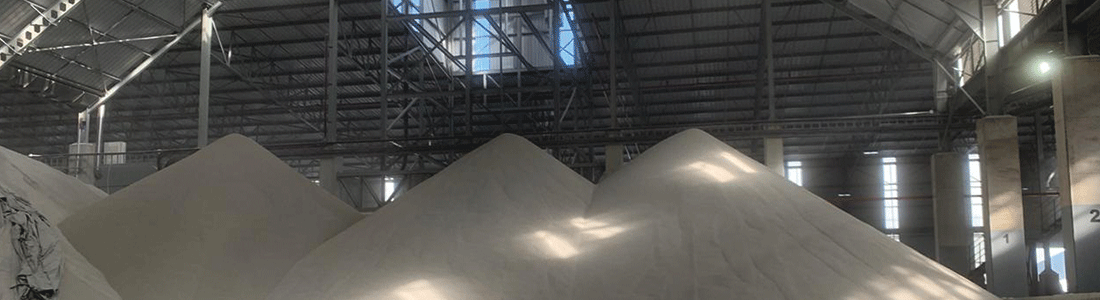
The challenge
The standard method of material handling found in South Africa is inefficient, threatening to cause product degradation due to the high contact of the fertiliser with machinery. Contact increases the risk of crushing the fertiliser, resulting in fine dust particles that decrease the product’s value while causing problems for farmers.
C. Steinweg Bridge needed to rebuild its facility after a massive fire in the Durban precinct in 2017. What was a considerable blow provided an opportunity to improve the company’s handling solutions and the control over the end product - the aim to give customers a higher quality product that is more profitable and more beneficial to the end-user.
The solution
C. Steinweg Bridge developed a new 60 000 m2 facility, purpose-built to cater to the needs of the fertiliser industry, with fewer touchpoints, less handling, and state-ofthe-art automation - unlike any other warehousing facility in Southern Africa. The new system has tipping points outside the facility. Conveyor belts then carry the material to a height and distribute it evenly into stockpiles. Roger Hogg, Managing Director of C. Steinweg Bridge, explains, “This means a machine is not required to push the material to create the stockpiles, as was done previously. The use of Nidec Control Techniques equipment has been instrumental in the efficiency of this new facility.”
Unidrive M400 powers the motors on the conveyors, crushers, and chutes. The drive provides maximum stability and control of induction motors at all outputs, improving throughput with advanced open-loop motor control algorithms. The drives are rated for heavy-duty and boast two Safe Torque Off terminals and an onboard PLC as standard.
M701 was applied as the PLC control master, supporting a wide range of feedback technologies and supplying advanced motor control. Additionally, for superior machine control, the MCi210 automation module was used. This module executes comprehensive programs that can control multiple drives and motors simultaneously across real-time networks. The MCi210 ensures higher performance by delivering two additional Ethernet ports with an internal switch, offering support for standard Ethernet protocols, and a faster exchange thanks to a parallel interface with a drive processor.
Nidec Control Technique’s Machine Control Studio automates the system, creating a flexible and intuitive environment for programming. The programming environment is fully IEC 61131-3 compliant, meaning that it was familiar and, therefore, fast and easy to use for the facility’s control engineers.
The benefits
“The technology from Nidec Control Techniques enables us to keep a close eye on our delivery, giving us data on tons per second. We are achieving more tons per square metre than any other facility known to us, with larger trucks moving more product, faster.” Roger Hogg, Managing Director of C. Steinweg Bridge.
“The SCADA system and data on what is happening at the facility will be instrumental in our business decisionmaking down the line. The information we gain from the digitalised system will be invaluable to us and our clients from a cost and efficiency perspective.” Roger Hogg, Managing Director of C. Steinweg Bridge.
Read the full case study:
Impressed? Contact us for your automation needs