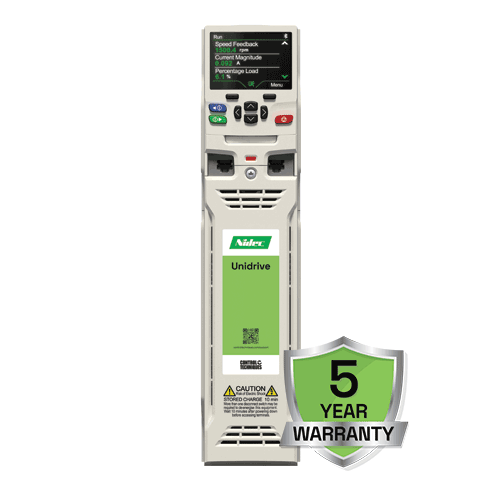
0.75 kW – 2.8 MW (1.0 - 4,200 hp)
200 V / 400 V / 575 V / 690 V
- Overview
- Specifications
- Options
- Downloads
High performance drive for open-loop control of induction, permanent-magnet, and hybrid PM motors
The M600 is the perfect choice for applications that require high performance open-loop control of induction or permanent magnet motors.
A comprehensive range of option modules are available for easy integration into all major fieldbus ecosystems and to tailor the drive to any application need.
*Obsessives included
Sensorless control for industrial processes
![]() Unidrive M supports sensorless control of induction, permanent-magnet, and hybrid PM motors, reducing system cost and improving robustness. |
|
![]() Unidrive M has been designed to bring improved energy efficiency to all applications, delivering up to 98% efficiency, minimising losses during the conversion process. |
|
![]() The M600 incorporates an onboard PLC which can execute Machine Control Studio (IEC61131-3) programs for logic control, sequencing, speed following and digital lock - removing the need for additional PLCs. Up to three System Integrator modules can be added for additional I/O or fieldbus communications. |
|
![]() All Unidrive M drives have integrated Safe Torque Off (STO) inputs, certified to SIL3 / PLe, providing an elegant and reliable safety solution. |
High power modular drives
Unidrive M’s modular offering gives you never before seen flexibility in building compact, reliable high-power solutions. Paralleled together, Unidrive M can control asynchronous and synchronous motors up to 2.8 MW (4,200 hp). At the top of the modular drives range, the Frame 12 is a 500 kW (700 hp) single module that delivers unmatched power density, while keeping both footprint and system costs to a minimum. The Unidrive M modules can be paralleled together into a wide range of flexible solutions to solve all system needs, including Active Front End and multi-pulse rectifier configurations.
Efficient system build
Designing and building a high power drive cubicle takes immense engineering knowhow. Most people don’t have that expertise in-house, but we do. And we’ve put it all into our DFS freestanding drives. The cubicle system is designed to make the most of our high power modular drives, benefiting the applications that need them the most. The results are maximum energy efficiency in an ingress protected package. Our cubicle drives come pre-assembled, easy to set up, with all necessary system components included. Furthermore, we can ship your Freestanding drive to you with a very short lead time, saving weeks on typical industry standards.
Functional safety
All Unidrive M drives have integrated dual Safe Torque Off (STO) inputs, certified to SIL3 / PLe, providing an elegant and reliable safety solution. The addition of an MiS210 safety option extends the built-in STO with the ability to safely monitor and/or restrict the scope of motion.
Safety functions include: STO, SBC, SOS, SS1, SS2, SLS, SSM, SLA, SDI, SLP & SES
For maximum flexibility in the safety system architecture, the modules support both wired and network safety connections: CIP-Safety on EtherNet/IP and Safety over EtherCAT (FSoE).
To find out more, visit our Functional Safety page.
Features
Enhanced throughput with high-performance open-loop control of induction and permanent magnet motors
- Advanced Rotor Flux Control (RFC) algorithm gives maximum stability and control of induction and permanent magnet motors
- 200% motor overload suitable for heavy industrial machinery applications
Reduce system costs by directly integrating with applications
- M600 incorporates an onboard PLC which can execute Machine Control Studio (IEC61131-3) programs for logic control, sequencing, speed following and digital lock - removing the need for additional PLCs
- Fit up to three SI modules to add safe motion, speed feedback, additional I/O and fieldbus communications
Software
![]() Connect is our latest drive configuration tool for commissioning, optimising and monitoring drive/system performance. Download |
|
![]() Control Techniques' Machine Control Studio provides a flexible and intuitive environment for programming new automation and motion control features. Download |
This product comes with 5-year warranty as standard
No registration. No extra cost. Just peace of mind from day one. Learn more.
Key data
- Heavy Duty rating: 0.75 kW – 2.8 MW (1.0 - 4,200 hp)
- Supply phases: 3 phase
Standard features
Intelligence:
- Onboard PLC
- Digital Lock Control
Onboard comms:
- RS485
Machine safety:
- 1 x Safe Torque Off (STO) terminal
- SIL3/PLe compliant
Keypad:
- No keypad as standard
Option slots:
- 3
Parameter cloning via:
- PC tools
- Smartcard
- SD card
Voltage ratings
200 V (200 V - 240 V ± 10%) |
400 V (380 V - 480 V ± 10%) |
575 V (500 V - 575 V ± 10%) |
575 V (500 V - 575 V ± 10%) |
690 V (500 V - 690 V ± 10%) |
Control mode
Open loop vector or V/Hz induction motor control |
Open loop Rotor Flux Control for induction motors (RFC-A) |
Open loop permanent magnet motor control (RFC-S) |
Open loop permanent magnet motor control (RFC-S) |
Closed loop Rotor Flux Control for induction motors (RFC-A) *Optional |
Active Front End (AFE) power quality convertor |
Single drives
FRAME |
DIMENSIONS |
WEIGHT |
||
mm |
in |
kg |
lb |
|
3 |
382 x 83 x 200 | 15.0 x 3.3 x 7.9 | 4.5 Max | 9.9 Max |
4 |
391 x 124 x 200 | 15.4 x 4.9 x 7.9 | 6.5 | 14.3 |
5 |
391 x 143 x 200 |
15.4 x 5.6 x 7.6 |
7.4 |
16.3 |
6 |
391 x 210 x 227 | 15.4 x 8.3 x 8.9 | 14 | 30.9 |
7 |
557 x 270 x 280 | 21.9 x 10.6 x 11.0 | 28 | 61.7 |
8 |
803 x 310 x 290 | 31.6 x 12.2 x 11.4 | 52 | 114.6 |
9A |
1108 x 310 x 290 | 43.6 x 12.2 x 11.4 | 66.5 | 146.6 |
9E |
1069 x 310 x 288 | 42.1 x 12.2 x 11.3 | 46 | 101.4 |
10E |
1069 x 310 x 288 | 42.1 x 12.2 x 11.3 | 46 | 101.4 |
11E |
1410 x 310 x 310 | 55.5 x 12.2 x 12.2 | 63 | 138.9 |
12 | 1750 x 295 x 526 |
68.9 x 11.6 x 20.7 |
AC to AC ('T' type): 130 DC to AC ('D' type): 113 |
287 249 |
All dimensions include mounting brackets
Modular drives
FRAME SIZE |
DIMENSIONS (H X W X D) |
|
---|---|---|
mm |
in |
|
INVERTER & RECTIFIER | ||
9A |
1108 x 310 x 290 | 43.62 x 12.21 x 11.4 |
9E | 9T |
1069 x 310 x 290 | 42.1 x 12.21 x 11.4 |
10E | 10T | 1069 x 310 x 290 | 42.1 x 12.21 x 11.4 |
11E | 11T |
1242 x 310 x 312 | 48.9 x 12.2 x 12.3 |
INVERTER | ||
9D |
773 x 310 x 290 | 30.4 x 12.2 x 11.4 |
10D |
773 x 310 x 290 | 30.4 x 12.2 x 11.4 |
11D |
863 x 310 x 290 | 34 x 12.2 x 12.3 |
RECTIFIER | ||
10A |
6 pulse
355 x 310 x 290
|
6 pulse
13.9 x 12.2 x 11.4
|
11A | 11T |
6 pulse |
6 pulse |
All dimensions include mounting brackets
Power and current ratings
The continuous current ratings given are for maximum 40 °C (104 °F), 1000 m altitude and 2 kHz switching frequency. Derating is required for higher switching frequencies, ambient temperature >40 °C (104 °F) and high altitude.
200 V (200 V to 240 V ±10%)
400 V (380 V to 480 V +/-10%)
Product Code M600/M700/M701/M702 |
Normal Duty | Heavy Duty | |||||
Supply Phases | Max Cont. Current (A) |
Motor Power (kW) |
Motor Power (HP) |
Max Cont. Current (A) |
Motor Power (kW) |
Motor Power (HP) |
|
Mxxx - 03400025A |
3 | 3.4 | 1.1 | 1.5 | 2.5 | 0.75 | 1 |
Mxxx - 03400031A |
3 | 4.5 | 1.5 | 2 | 3.1 | 1.1 | 1.5 |
Mxxx - 03400045A |
3 | 6.2 | 2.2 | 3 | 4.5 | 1,5 | 2 |
Mxxx - 03400062A |
3 | 7.7 | 3 | 5 | 6.2 | 2.2 | 3 |
Mxxx - 03400078A |
3 | 10.4 | 4 | 5 | 7.8 | 3 | 5 |
Mxxx - 03400100A |
3 | 12.3 | 5.5 | 7.5 | 10 | 4 | 5 |
Mxxx - 04400150A |
3 | 18.5 | 7.5 | 10 | 15 | 5.5 | 10 |
Mxxx - 04400172A |
3 | 24 | 11 | 15 | 17.2 | 7.5 | 10 |
Mxxx - 05400270A |
3 | 30 | 15 | 20 | 27 | 11 | 20 |
Mxxx - 05400300A |
3 | 31 | 15 | 20 | 30 | 15 | 20 |
Mxxx - 06400350A |
3 | 38 | 18.5 | 25 | 35 | 15 | 25 |
Mxxx - 06400420A |
3 | 48 | 22 | 30 | 42 | 18.5 | 30 |
Mxxx - 06400470A |
3 | 63 | 30 | 40 | 47 | 22 | 30 |
Mxxx - 07400660A |
3 | 79 | 37 | 50 | 66 | 30 | 50 |
Mxxx - 07400770A |
3 | 94 | 45 | 60 | 77 | 37 | 60 |
Mxxx - 07401000A |
3 | 112 | 55 | 75 | 100 | 45 | 75 |
Mxxx - 08401340A |
3 | 155 | 75 | 100 | 134 | 55 | 100 |
Mxxx - 08401570A |
3 | 184 | 90 | 125 | 157 | 75 | 125 |
Mxxx - 09402000A |
3 | 221 | 110 | 150 | 200 | 90 | 150 |
Mxxx - 09402240A |
3 | 266 | 132 | 200 | 224 | 110 | 150 |
Mxxx - 09402000E |
3 | 221 | 110 | 150 | 200 | 90 | 150 |
Mxxx - 09402240E |
3 | 266 | 132 | 200 | 224 | 110 | 150 |
Mxxx - 10402700E |
3 | 320 | 160 | 250 | 270 | 132 | 200 |
Mxxx - 10403200E |
3 | 361 | 200 | 300 | 320 | 160 | 250 |
Mxxx - 11403770E |
3 | 437 | 225 | 350 | 377 | 185 | 300 |
Mxxx - 11404170E |
3 | 487 | 250 | 400 | 417 | 200 | 350 |
Mxxx - 11404640E |
3 | 507 | 280 | 450 | 464 | 250 | 400 |
Mxxx -12404800 |
3 | 608 | 315 | 500 | 480 | 250 | 400 |
Mxxx -12405660 |
3 | 660 | 355 | 550 | 566 | 315 | 450 |
Mxxx -12406600 |
3 | 755 | 400 | 650 | 6602 | 355 | 550 |
Mxxx -12407200 |
3 | 8651 |
500 | 700 | 7203 | 400 | 600 |
Note1 110 % Overload at 30˚C and below and No Overload above that.
Note2 140 % Overload at 35˚C and below and 125% above that.
Note3 140 % Overload at 30˚C and below and 125% above that.
575 V (500 V to 575 V +/-10%)
Product Code M600/M700/M701/M702 |
Normal Duty | Heavy Duty | |||||
Supply Phases | Max Cont. Current (A) |
Motor Power (kW) |
Motor Power (HP) |
Max Cont. Current (A) |
Motor Power (kW) |
Motor Power (HP) |
|
Mxxx - 05500030A |
3 | 3.9 | 2.2 | 3 | 3 | 1.5 | 2 |
Mxxx - 05500040A |
3 | 6.1 | 4 | 5 | 4 | 2.2 | 3 |
Mxxx - 05500069A |
3 | 10 | 5.5 | 7.5 | 6.9 | 4 | 5 |
Mxxx - 06500100A |
3 | 12 | 7.5 | 10 | 10 | 5.5 | 7.5 |
Mxxx - 06500150A |
3 | 17 | 11 | 15 | 15 | 7.5 | 10 |
Mxxx - 06500190A |
3 | 22 | 15 | 20 | 19 | 11 | 15 |
Mxxx - 06500230A |
3 | 27 | 18.5 | 25 | 23 | 15 | 20 |
Mxxx - 06500290A |
3 | 34 | 22 | 30 | 29 | 18.5 | 25 |
Mxxx - 06500350A |
3 | 43 | 30 | 40 | 35 | 22 | 30 |
Mxxx - 07500440A |
3 | 53 | 45 | 50 | 44 | 30 | 40 |
Mxxx - 07500550A |
3 | 73 | 55 | 60 | 55 | 37 | 50 |
Mxxx - 08500630A |
3 | 86 | 75 | 75 | 63 | 45 | 60 |
Mxxx - 08500860A |
3 | 108 | 90 | 100 | 86 | 55 | 75 |
Mxxx - 09501040A |
3 | 125 | 110 | 125 | 104 | 77 | 100 |
Mxxx - 09501310A |
3 | 150 | 110 | 150 | 131 | 90 | 125 |
Mxxx - 09501040E |
3 | 125 | 110 | 125 | 104 | 75 | 100 |
Mxxx - 09501310E |
3 | 150 | 110 | 150 | 131 | 90 | 125 |
Mxxx - 10501520E |
3 | 200 | 130 | 200 | 152 | 110 | 150 |
Mxxx - 10501900E |
3 | 200 | 150 | 200 | 190 | 132 | 200 |
Mxxx - 11502000E |
3 | 248 | 185 | 250 | 200 | 150 | 200 |
Mxxx - 11502540E |
3 | 288 | 225 | 300 | 254 | 185 | 250 |
Mxxx - 11502850E |
3 | 315 | 250 | 350 | 285 | 225 | 300 |
Mxxx-12503150 |
3 | 376 | 250 | 350 | 315 |
250 |
350 |
Mxxx-12503600 |
3 | 428 | 300 | 400 | 360 | 250 | 350 |
Mxxx-12504100 |
3 | 480 | 330 | 450 | 410 |
300 |
400 |
Mxxx-12504600 |
3 | 532 | 370 | 500 | 460 | 330 |
450 |
690 V (500 V to 690 V +/-10%)
Product Code M600/M700/M701/M702 |
Normal Duty | Heavy Duty | |||||
Supply Phases | Max Cont. Current (A) |
Motor Power (kW) |
Motor Power (HP) |
Max Cont. Current (A) |
Motor Power (kW) |
Motor Power (HP) |
|
Mxxx - 07600190A |
3 | 23 | 18.5 | 25 | 19 | 15 | 20 |
Mxxx - 07600240A |
3 | 30 | 22 | 30 | 24 | 18.5 | 25 |
Mxxx - 07600290A |
3 | 36 | 30 | 40 | 29 | 22 | 30 |
Mxxx - 07600380A |
3 | 46 | 37 | 50 | 38 | 30 | 40 |
Mxxx - 07600440A |
3 | 52 | 45 | 60 | 44 | 37 | 50 |
Mxxx - 07600540A |
3 | 73 | 55 | 75 | 54 | 45 | 60 |
Mxxx - 08600630A |
3 | 86 | 75 | 100 | 63 | 55 | 75 |
Mxxx - 08600860A |
3 | 108 | 90 | 125 | 86 | 75 | 100 |
Mxxx - 09601040A |
3 | 125 | 110 | 150 | 104 | 90 | 125 |
Mxxx - 09601310A |
3 | 150 | 132 | 175 | 131 | 110 | 150 |
Mxxx - 09601040E |
3 | 125 | 110 | 150 | 104 | 90 | 125 |
Mxxx - 09601310E |
3 | 155 | 132 | 175 | 131 | 110 | 150 |
Mxxx - 10601500E |
3 | 172 | 160 | 200 | 150 | 132 | 175 |
Mxxx - 10601780E |
3 | 197 | 185 | 250 | 178 | 160 | 200 |
Mxxx - 11602100E |
3 | 225 | 200 | 250 | 210 | 185 | 250 |
Mxxx - 11602380E |
3 | 275 | 250 | 300 | 238 | 200 | 250 |
Mxxx-12603150 |
3 | 376 | 355 | 450 | 315 | 280 | 400 |
Mxxx-12603600 |
3 | 428 | 400 | 500 | 360 | 355 | 450 |
Mxxx-12604100 |
3 | 480 | 450 | 600 | 410 | 400 |
500 |
Mxxx-12604600 |
3 | 532 | 500 | 650 | 460 | 450 | 600 |