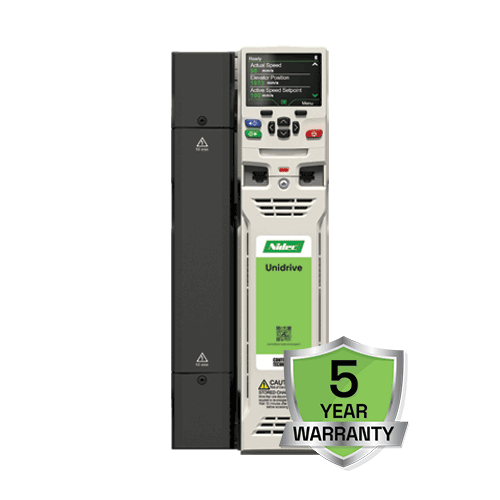
0 - 1,250 Hz Closed Loop
0.75 kW – 2.8 MW (1.0 - 4,200 hp)
200 V / 400 V / 575 V / 690 V
- Overview
- Specifications
- Options
- Downloads
Unidrive HS70 provides maximum control of high speed motors and incorporates an onboard Advanced Motion Controller and onboard PLC.
Maximise throughput with superior motor control
- High bandwidth motor control algorithm for closed-loop induction, permanent magnet and servo motors - 3,000 Hz current loop bandwidth and - 1,250 Hz speed loop bandwidth
- Flexible speed and position feedback interface supports a wide range of feedback technologies from robust resolvers to high resolution encoders
- Up to three encoder channels simultaneously e.g. 1 feedback encoder, 1 reference encoder and 1 simulated output
- MCi modules can eliminate the need for external PLCs and motion controllers
- Simulated encoder output can provide position reference for CAMs, digital lock and electronic gearbox applications
Optimise system performance with onboard Advanced Motor Controller
- HS70 incorporates an Advanced Motion Controller capable of controlling 1.5 axes. The motion functions are carried out 'on the drive' so that system performance is maximised
Design flexible centralised and decentralised control systems
- MCi modules can be added to execute larger programs for advanced system control capability
- Onboard PLC for logic programs
- Machine Control Studio is an industry standard IEC61131-3 programming environment for efficient system design and configuration
- Integrated dual port Ethernet switch provides simple connectivity using standard connections
- Onboard real-time Ethernet (IEEE 1588 V2) uses RTMoE (Real Time Motion over Ethernet) to provide fast communication and accurate axis synchronisation
- Three System Integration ports are available to fit additional fieldbus, position feedback and I/O options
Conform to safety standards, maximise uptime and reduce costs by integrating directly with safety systems
- HS70 has an integrated Safe Torque Off (STO) input and can accommodate an SI-Safety module for safe motion functions
Software
![]() Connect is our latest drive configuration tool for commissioning, optimising and monitoring drive/system performance. Download |
|
![]() Control Techniques' Machine Control Studio provides a flexible and intuitive environment for programming new automation and motion control features. Download |
This product comes with 5-year warranty as standard
No registration. No extra cost. Just peace of mind from day one. Learn more.
Key data
- Heavy Duty rating: 0.75 kW – 2.8 MW (1.0 - 4,200 hp)
- Supply phases: 3 phase
Standard features
Intelligence:
- Onboard PLC
- Advanced Motion Controller
Onboard comms:
- HS70 & HS72 – Ethernet
- HS71 – RS485
Feedback:
- 2 x Encoder inputs
- 1 x Simulated encoder output
Machine safety:
- HS70 & HS71 - 1 x Safe Torque Off (STO) terminal
- HS72 – 2 x STO terminals
- SIL3/PLe compliant
Keypad:
- No keypad as standard
Option slots:
- 3
Parameter cloning via:
- PC tools
- Smartcard
- SD card
VOLTAGE RATING | POWER RANGE | ||
---|---|---|---|
100 V (100 V - 120 V ± 10%) | |||
200 V (200 V - 240 V ± 10%) | ✓ | 0.75-37 kW | |
400 V (380 V - 480 V ± 10%) | ✓ | 0.75-75 kW | |
575 V (500 V - 575 V ± 10%) | ✓ | 75 - 225 kW | |
690 V (500 V - 690 V ± 10%) | ✓ | 90 - 250 kW |
CONTROL MODE |
|
Open loop vector or V/Hz induction motor control |
✓ |
Open loop Rotor Flux Control for induction motors (RFC-A) |
✓ |
Open loop permanent magnet motor control (RFC-S) |
✓ |
Closed loop Rotor Flux Control for induction motors (RFC-A) |
✓ |
Closed loop permanent magnet motor control (RFC-S) |
✓ |
Active Front End (AFE) power quality convertor |
✓ |
SINGLE DRIVES:
FRAME SIZE |
DIMENSIONS (H X W X D) |
WEIGHT |
||
mm |
in |
kg |
lb |
|
3 |
382 x 83 x 200 | 15.0 x 3.3 x 7.9 | 4.5 Max | 9.9 Max |
4 |
391 x 124 x 200 | 15.4 x 4.9 x 7.9 | 6.5 | 14.3 |
5 |
391 x 143 x 200 |
15.4 x 5.6 x 7.6 |
7.4 |
16.3 |
6 |
391 x 210 x 227 | 15.4 x 8.3 x 8.9 | 14 | 30.9 |
7 |
557 x 270 x 280 | 21.9 x 10.6 x 11.0 | 28 | 61.7 |
8 |
803 x 310 x 290 | 31.6 x 12.2 x 11.4 | 52 | 114.6 |
9A |
1108 x 310 x 290 | 43.6 x 12.2 x 11.4 | 66.5 | 146.6 |
9E |
1069 x 310 x 288 | 42.1 x 12.2 x 11.3 | 46 | 101.4 |
10E |
1069 x 310 x 288 | 42.1 x 12.2 x 11.3 | 46 | 101.4 |
11E |
1410 x 310 x 310 | 55.5 x 12.2 x 12.2 | 63 | 138.9 |
MODULAR DRIVES:
FRAME SIZE | DIMENSIONS (H X W X D) | WEIGHT | ||
---|---|---|---|---|
mm | in | kg | lb | |
INVERTER & RECTIFIER | ||||
9A | 1108 x 310 x 290 | 43.62 x 12.21 x 11.4 | 66.5 | 146.6 |
9E | 9T | 1069 x 310 x 290 | 42.1 x 12.2 x 11.4 | 46 | 60 | 101.4 | 132.3 |
10E | 10T | 1069 x 310 x 290 | 42.1 x 12.2 x 11.4 | 46 | 60 | 101.4 | 132.3 |
11E | 11T | 1242x 310 x 312 | 48.9 x 12.2 x 12.3 | 63 | 65 | 138.9 | 143.3 |
INVERTER | ||||
9D | 773 x 310 x 290 | 30.4 x 12.2 x 11.4 | 34 | 75 |
10D | 773 x 310 x 290 | 30.4 x 12.2 x 11.4 | 34 | 75 |
11D | 863 x 310 x 312 | 34 x 12.2 x 12.3 | 42 | 92.6 |
RECTIFIER | ||||
10A |
6 pulse
355 x 310 x 290
|
6 pulse
15.8 x 12.2 x 11.4
|
12 | 26.5 |
11A | 11T |
6 pulse
415 x 310 x 290
12 pulse
415 x 310 x 290
|
6 pulse
16.3 x 12.2 x 11.4
12 pulse
16.3 x 12.2 x 11.4
|
21 | 23 | 46.3 | 50.7 |
All dimensions include mounting brackets