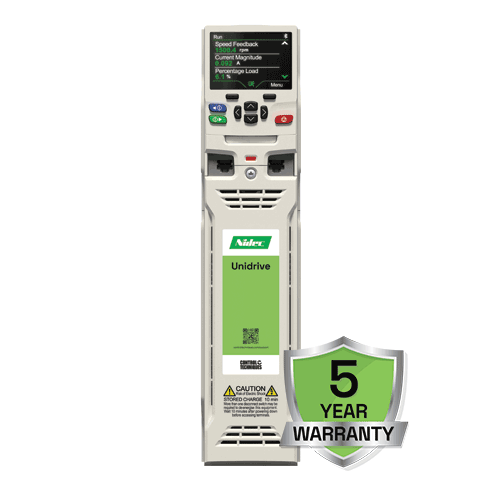
0.75 kW - 2.8 MW Heavy Duty (1.0 hp - 4,200 hp)
200 V | 400 V | 575 V | 690 V
- Overview
- Specifications
- Options
- Downloads
The ultimate universal drive
Our Unidrive M700 drives offer the highest control stability and bandwidth for every industrial motor type.
Unidrive M enables maximum machine throughput in every application and with every motor, from AC induction motors to dynamic linear motors and from energy saving hybrid permanent-magnet motors to high performance servo motors.
*Obsessives included
The drive for your industry and application
|
|
![]()
|
|
![]()
|
High power drives
High power modular drives
Unidrive M’s modular offering gives you never before seen flexibility in building compact, reliable high-power solutions. Paralleled together, Unidrive M can control asynchronous and synchronous motors up to 2.8 MW (4,200 hp). At the top of the modular drives range, the Frame 12 is a 500 kW (700 hp) single module that delivers unmatched power density, while keeping both footprint and system costs to a minimum. The Unidrive M modules can be paralleled together into a wide range of flexible solutions to solve all system needs, including Active Front End and multi-pulse rectifier configurations.
Efficient system build
Designing and building a high power drive cubicle takes immense engineering knowhow. Most people don’t have that expertise in-house, but we do. And we’ve put it all into our DFS freestanding drives. The cubicle system is designed to make the most of our high power modular drives, benefiting the applications that need them the most. The results are maximum energy efficiency in an ingress protected package. Our cubicle drives come pre-assembled, easy to set up, with all necessary system components included. Furthermore, we can ship your Freestanding drive to you with a very short lead time, saving weeks on typical industry standards.
Multi-protocol - network communications
A single drive that does it all...
Control Techniques’ philosophy has always been to support innovators, regardless of which communications protocol they may use. It’s for them that we’ve developed the most flexible high performance drive platform on the market.
Having multiple protocols supported by one drive means that different systems can share one design, reducing engineering effort and complexity, and helping to rationalise inventory of parts and spares. But we didn’t stop there. Today Unidrive M series drives offer EtherNet/IP, Modbus/TCP, RTMoE and PROFINET RT as standard, on a single drive platform, simultaneously. With this, Unidrive M delivers even more performance and extends the range of supported applications and achievable topologies. Using only the standard on-board communications it is possible to connect an HMI via Modbus TCP/IP, simultaneously with a high performance connection to a central PLC using EtherNet/IP or PROFINET RT.
RTMoE
Real-Time Motion over Ethernet (RTMoE) is included as standard on Unidrive M700 and M702 drives. It provides synchronised communication between drives at 250 μs cycle time, using the Precision Time Protocol as defined by IEEE1588 V2. Inter-axis synchronisation using RTMoE delivers the ability to implement complex, highly accurate electronic line-shaft applications without the need for a powerful PLC. Therefore it's all at a fraction of the cost of other solutions available on the market today.
Traffic management
Every Ethernet based Unidrive incorporates dedicated network switches that allow the drives to be conveniently daisychained together; reducing the system wiring cost and saving valuable panel space. Using these dedicated switches also means that traffic on the network is perfectly managed to prevent network overload and the inherent performance degradation that may otherwise bane similar systems.
Cost-optimised integration
The diagram below gives an illustration of the flexibility that Unidrive can bring, exploiting the high performance, cost effective features of RTMoE simultaneously with the supervisory control offered by a traditional PLC.
Functional safety
All Unidrive M drives have integrated dual Safe Torque Off (STO) inputs, certified to SIL3 / PLe, providing an elegant and reliable safety solution.
The addition of an MiS210 safety option extends the built-in STO with the ability to safely monitor and/or restrict the scope of motion.
Safety functions include: STO, SBC, SOS, SS1, SS2, SLS, SSM, SLA, SDI, SLP & SES.
For maximum flexibility in the safety system architecture, the modules support both wired and network safety connections: CIP-Safety on EtherNet/IP and Safety over EtherCAT (FSoE).
To find out more, visit our Functional Safety page.
Features
Feedback
The built-in, ultra-flexible speed and position feedback interface supports a wide range of feedback technologies from robust resolvers to high resolution encoders, including SinCos, EnDat, SSI, HIPERFACE and BiSS.
Sensorless
Unidrive supports sensorless control of induction, permanent-magnet, and hybrid PM motors, reducing system cost and improving robustness.
High performance and high power
With Unidrive there is no compromise between power and control performance. Unidrive supports high output switching frequencies throughout the power range, making it the drive of choice when your application demands uncompromised high performance control at high powers.
Control
High bandwidth motor control supporting switching frequencies up to 16 kHz, for open and closed loop induction, servo and hybrid PM motors, giving up to 3,000 Hz current loop bandwidth and 250 Hz speed loop bandwidth. Unidrive, with its high speed variants, is suitable for applications where output frequencies above 600 Hz are needed, such as spindles and centrifuges.
Universally applicable
Having one universal drive in control of multiple parts of the application radically simplifies machine design. Your engineering team only have one product to learn, allowing them to spend more time on other tasks. It also means a single, universal replacement for any maintenance, repair or operational need.
Integrated safety
Modernising system design, replacing traditional electro-mechanical safety components with the capabilities of the latest generation of variable speed drives, is the new standard across industries to increase efficiency and availability.
Unidrive offers integrated single or dual Safe Torque Off (STO) inputs, certified to SIL3 / PLe, providing an elegant and more reliable solution over traditional motor contactors.
On-board PLC
All Unidrive M series drives incorporate an easy to use, onboard PLC which can execute programs for logic and IEC 61131-3 motion and sequencing with real-time tasks.
Advanced motor controller
The Unidrive M700 series integrates a 1.5 axes Advanced Motion Controller, allowing motion functions to be synchronously carried out on the drive at 250 μs cycle time, minimising system latencies and maximising performance. By implementing motion control on the drive, the system design can be liberated from being tied to specific PLC vendors, at the same time reducing the computational load on the external PLC or even replacing it altogether.
Key features of the Advanced Motion Controller include:
- 250 μs cycle time
- Motion profile generator
- Electronic gearbox
- Simple cam profiles with point-to-point selectable interpolation
- Homing functions
- High speed position freeze (Touch probe)
MCi integrated machine controllers
Second processor for PLC programs and multi-axis control
MCi modules add a powerful second processor to Unidrive M, extending the drive’s system and machine control capabilities to run application programs up to four times faster than a standard PLC.
MCi programs can access and manage Unidrive M’s embedded Advanced Motion Controller across a wide range of networks, providing perfectly synchronised multi-axis machine performance.
The modules are powered from the drives internal power supply, which means less wiring and less physical space is required. They work seamlessly with external components such as I/O, HMIs and other networked drives through Unidrive M’s native communication ports and System Integration modules.
The MCi210 also provides two additional Ethernet ports with an internal network switch.
Software
![]() Connect is our latest drive configuration tool for commissioning, optimising and monitoring drive/system performance. Download |
|
![]() Control Techniques' Machine Control Studio provides a flexible and intuitive environment for programming new automation and motion control features. Download |
This product comes with 5-year warranty as standard
No registration. No extra cost. Just peace of mind from day one. Learn more.
Environmental safety and electrical conformance
IP20 / NEMA1 / UL TYPE 1 (UL open class as standard, additional kit needed to achieve Type 1) |
Frames 3 to 8 achieve IP65 / NEMA4 / UL TYPE 12 rating on the rear of the drive when through panel mounted |
Frames 9, 10 & 11 achieve IP55 / NEMA4 / UL TYPE 12 rating on the rear of the drive when through panel mounted |
Ambient temperature -20 °C to 40 °C (-4 °F to 104 °F) as standard. Up to 55 °C (131 °F) with derating |
Humidity 95 % maximum (non-condensing) at 40 °C (104 °F) |
Altitude: 0 to 3000 m (9900 ft), derate 1 % per 100 m (330 ft) between 1000 m (3300 ft) and 3000 m (9900 ft) |
Random Vibration: Tested in accordance with IEC 60068-2-64 |
Mechanical Shock Tested in accordance with IEC 60068-2-29 |
Storage temperature -40 °C to 55 °C (-40 °F to 131 °F) or up to 70 °C (158 °F) for short-term storage |
Electromagnetic Immunity complies with EN 61800-3 and EN 61000-6-2 |
With onboard EMC filter, complies with EN 61800-3 (2nd environment) |
EN/IEC 61000-6-3 and EN/IEC 61000-6-4 with optional footprint EMC filter |
EN/IEC 61800-5-1 (Electrical Safety) |
EN/IEC 61131-2 I/O |
Safe Torque Off, independently assessed by TÜV to IEC 61800-5-2 SIL 3 and EN ISO 13849-1 PLe |
UL 508C (Electrical Safety) |
Features and specifications table
M700 | M701 | M702 | ||
Performance | Current loop update: 62 μs |
✓ | ✓ | ✓ |
Heavy Duty peak rating: 200 % (3 s) |
✓ | ✓ | ✓ | |
Maximum output frequency: 599 Hz (open loop), 550 Hz (RFC-A & RFC-S) |
✓ |
✓ | ✓ | |
Switching frequency range: 2, 3, 4, 6, 8, 12, 16 kHz (3 kHz default) |
✓ | ✓ | ✓ | |
High performance current controllers - |
✓ | ✓ | ✓ | |
On-board intelligence |
Programmable Logic Control (PLC) |
✓ | ✓ |
✓ |
Real-time tasks |
✓ |
✓ | ✓ | |
Digital lock control |
✓ |
✓ | ✓ | |
Advanced Motion Controller - |
✓ | ✓ | ✓ | |
On-board comms |
Ethernet (2 switched ports): EtherNet/IP, Modbus/TCP, RTMoE and PROFINET RT - |
✓ | - | ✓ |
RS485: Modbus RTU |
- | ✓ | - | |
Mechanical attributes Tile mounting on sizes 3, 4, 5 |
✓ |
✓ | ✓ | |
Unidrive SP compatible mechanical footprint |
✓ |
✓ | ✓ | |
Common DC bus connections |
✓ |
✓ | ✓ | |
Parameter back-up |
Ethernet |
✓ | - | ✓ |
Serial port cloning |
✓ |
✓ | ✓ | |
SD card (using SD-Card Adaptor) |
✓ |
✓ | ✓ | |
Smartcard reader support |
✓ |
✓ | ✓ | |
Electronic motor nameplate parameter storage (HIPERFACE, EnDat 2.2) |
✓ |
✓ | ✓ | |
Feedback |
Encoder and resolver feedback input |
2 | 2 | 2 |
Simulated encoder output |
1 | 1 | 1 | |
Optional SI-Encoder/SI-Universal Encoder |
✓ |
✓ | ✓ | |
On-board I/O |
Analogue input |
3 | 3 | - |
Analogue output |
2 | 2 | - | |
Digital input |
3 | 3 | 2* | |
Digital output |
- | - | 2 | |
Bidirectional digital input or output |
3 | 3 | - | |
Relay output |
1 | 1 | 1 | |
Machine Safety Single-channel Safe Torque Off (STO) input, certified to SIL3 / PLe |
✓ |
✓ | - | |
Dual-channel Safe Torque Off (STO) inputs, certified to SIL3 / PLe |
- | - | ✓ | |
Power and motor control | Stationary autotune for permanent magnet motors |
✓ |
✓ | ✓ |
Mechanical load resonance compensation |
✓ |
✓ | ✓ | |
Wide operating range back-up DC supply | ✓ |
✓ | ✓ | |
24 V control back-up |
✓ |
✓ | ✓ | |
Other | Temperature controlled fan operation with user adjustable speed limit |
✓ |
✓ | ✓ |
User replaceable fan(s) |
✓ |
✓ | ✓ | |
Conformal coating |
✓ |
✓ | ✓ | |
Standby mode (energy saving) |
✓ |
✓ | ✓ |
*Terminal 8 on the Unidrive M702, by default, is set as a digital input but can be configured as a motor protection thermistor input
Overload ratings by operating mode
Operating mode |
RFC from cold |
RFC from 100 % |
Open loop from cold | Open loop from 100 % |
Normal duty overload with motor rated current = drive rated current | 110 % for 165 s |
110 % for 9 s |
110% for 165 s |
110% for 9 s |
Heavy duty overload with motor rated current = drive rated current (size 8 and below) |
200 % for 28 s |
200 % for 3 s |
150 % for 60 s |
150% for 7 s |
Heavy duty overload with motor rated current = drive rated current (size 9A, 9E, 10, 11 and 12) |
170 % for 42 s |
170 % for 5 s |
150 % for 60 s |
150% for 7 s |
Heavy duty overload with motor rated current = drive rated current (size 12) |
140 % for 60 s |
140 % for 10 s |
140 % for 60 s |
140 % for 10 s |
Ordering guide
DC Bus Choke/AC Line Choke | ||||
Frame size |
Dimensions H x W x D mm (in) |
Weight kg (lb) |
Internal |
External |
3 | 365 x 83 x 200 (14.4 x 3.3 x 7.9) |
4.5 (9.9) |
✓ |
- |
4 | 365 x 124 x 200 (14.4 x 4.9 x 7.9) |
6.5 (14.3) |
✓ |
- |
5 | 365 x 143 x 200 (14.4 x 5.6 x 7.6) |
7.4 (16.3) |
✓ |
- |
6 | 365 x 210 x 227 (14.4 x 8.3 x 8.9) |
14 (30.9) |
✓ |
- |
7 | 508 x 270 x 280 (20 x 10.6 x 11.0) |
28 (61.7) |
✓ |
- |
8 | 753 x 310 x 290 (29.7 x 12.2 x 11.4) |
52 (114.6) |
✓ |
- |
9A | 1049 x 310 x 290 (41.3 x 12.2 x 11.4) |
66.5 (146.6) |
✓ |
|
9E | 1010 x 310 x 290 (41.3 x 12.2 x 11.4) |
46 (101.4) |
- | ✓ |
10E | 1010 x 310 x 290 (41.3 x 12.2 x 11.4) |
46 (101.4) |
- | ✓ |
11E | 1190 x 310 x 312 (46.9 x 12.2 x 12.3) |
63 (138.9) |
- | ✓ |
12 | 1750 x 295 x 526 (68.9 x 11.6 x 20.7) |
AC to AC ('T' type): 130 kg (287 lb) DC to AC ('D' type): 113 kg (249 lb) |
- | ✓ |
Power and current ratings
The continuous current ratings given are for maximum 40 °C (104 °F), 1000 m altitude and 2 kHz switching frequency. Derating is required for higher switching frequencies, ambient temperature >40 °C (104 °F) and high altitude.
200 V (200 V to 240 V ±10%)
400 V (380 V to 480 V +/-10%)
Product Code M600/M700/M701/M702 |
Normal Duty | Heavy Duty | |||||
Supply Phases | Max Cont. Current (A) |
Motor Power (kW) |
Motor Power (HP) |
Max Cont. Current (A) |
Motor Power (kW) |
Motor Power (HP) |
|
Mxxx - 03400025A |
3 | 3.4 | 1.1 | 1.5 | 2.5 | 0.75 | 1 |
Mxxx - 03400031A |
3 | 4.5 | 1.5 | 2 | 3.1 | 1.1 | 1.5 |
Mxxx - 03400045A |
3 | 6.2 | 2.2 | 3 | 4.5 | 1,5 | 2 |
Mxxx - 03400062A |
3 | 7.7 | 3 | 5 | 6.2 | 2.2 | 3 |
Mxxx - 03400078A |
3 | 10.4 | 4 | 5 | 7.8 | 3 | 5 |
Mxxx - 03400100A |
3 | 12.3 | 5.5 | 7.5 | 10 | 4 | 5 |
Mxxx - 04400150A |
3 | 18.5 | 7.5 | 10 | 15 | 5.5 | 10 |
Mxxx - 04400172A |
3 | 24 | 11 | 15 | 17.2 | 7.5 | 10 |
Mxxx - 05400270A |
3 | 30 | 15 | 20 | 27 | 11 | 20 |
Mxxx - 05400300A |
3 | 31 | 15 | 20 | 30 | 15 | 20 |
Mxxx - 06400350A |
3 | 38 | 18.5 | 25 | 35 | 15 | 25 |
Mxxx - 06400420A |
3 | 48 | 22 | 30 | 42 | 18.5 | 30 |
Mxxx - 06400470A |
3 | 63 | 30 | 40 | 47 | 22 | 30 |
Mxxx - 07400660A |
3 | 79 | 37 | 50 | 66 | 30 | 50 |
Mxxx - 07400770A |
3 | 94 | 45 | 60 | 77 | 37 | 60 |
Mxxx - 07401000A |
3 | 112 | 55 | 75 | 100 | 45 | 75 |
Mxxx - 08401340A |
3 | 155 | 75 | 100 | 134 | 55 | 100 |
Mxxx - 08401570A |
3 | 184 | 90 | 125 | 157 | 75 | 125 |
Mxxx - 09402000A |
3 | 221 | 110 | 150 | 200 | 90 | 150 |
Mxxx - 09402240A |
3 | 266 | 132 | 200 | 224 | 110 | 150 |
Mxxx - 09402000E |
3 | 221 | 110 | 150 | 200 | 90 | 150 |
Mxxx - 09402240E |
3 | 266 | 132 | 200 | 224 | 110 | 150 |
Mxxx - 10402700E |
3 | 320 | 160 | 250 | 270 | 132 | 200 |
Mxxx - 10403200E |
3 | 361 | 200 | 300 | 320 | 160 | 250 |
Mxxx - 11403770E |
3 | 437 | 225 | 350 | 377 | 185 | 300 |
Mxxx - 11404170E |
3 | 487 | 250 | 400 | 417 | 200 | 350 |
Mxxx - 11404640E |
3 | 507 | 280 | 450 | 464 | 250 | 400 |
Mxxx -12404800 |
3 | 608 | 315 | 500 | 480 | 250 | 400 |
Mxxx -12405660 |
3 | 660 | 355 | 550 | 566 | 315 | 450 |
Mxxx -12406600 |
3 | 755 | 400 | 650 | 6602 | 355 | 550 |
Mxxx -12407200 |
3 | 8651 |
500 | 700 | 7203 | 400 | 600 |
Note1 110 % Overload at 30ËšC and below and No Overload above that.
Note2 140 % Overload at 35ËšC and below and 125% above that.
Note3 140 % Overload at 30ËšC and below and 125% above that.
575 V (500 V to 575 V +/-10%)
Product Code M600/M700/M701/M702 |
Normal Duty | Heavy Duty | |||||
Supply Phases | Max Cont. Current (A) |
Motor Power (kW) |
Motor Power (HP) |
Max Cont. Current (A) |
Motor Power (kW) |
Motor Power (HP) |
|
Mxxx - 05500030A |
3 | 3.9 | 2.2 | 3 | 3 | 1.5 | 2 |
Mxxx - 05500040A |
3 | 6.1 | 4 | 5 | 4 | 2.2 | 3 |
Mxxx - 05500069A |
3 | 10 | 5.5 | 7.5 | 6.9 | 4 | 5 |
Mxxx - 06500100A |
3 | 12 | 7.5 | 10 | 10 | 5.5 | 7.5 |
Mxxx - 06500150A |
3 | 17 | 11 | 15 | 15 | 7.5 | 10 |
Mxxx - 06500190A |
3 | 22 | 15 | 20 | 19 | 11 | 15 |
Mxxx - 06500230A |
3 | 27 | 18.5 | 25 | 23 | 15 | 20 |
Mxxx - 06500290A |
3 | 34 | 22 | 30 | 29 | 18.5 | 25 |
Mxxx - 06500350A |
3 | 43 | 30 | 40 | 35 | 22 | 30 |
Mxxx - 07500440A |
3 | 53 | 45 | 50 | 44 | 30 | 40 |
Mxxx - 07500550A |
3 | 73 | 55 | 60 | 55 | 37 | 50 |
Mxxx - 08500630A |
3 | 86 | 75 | 75 | 63 | 45 | 60 |
Mxxx - 08500860A |
3 | 108 | 90 | 100 | 86 | 55 | 75 |
Mxxx - 09501040A |
3 | 125 | 110 | 125 | 104 | 77 | 100 |
Mxxx - 09501310A |
3 | 150 | 110 | 150 | 131 | 90 | 125 |
Mxxx - 09501040E |
3 | 125 | 110 | 125 | 104 | 75 | 100 |
Mxxx - 09501310E |
3 | 150 | 110 | 150 | 131 | 90 | 125 |
Mxxx - 10501520E |
3 | 200 | 130 | 200 | 152 | 110 | 150 |
Mxxx - 10501900E |
3 | 200 | 150 | 200 | 190 | 132 | 200 |
Mxxx - 11502000E |
3 | 248 | 185 | 250 | 200 | 150 | 200 |
Mxxx - 11502540E |
3 | 288 | 225 | 300 | 254 | 185 | 250 |
Mxxx - 11502850E |
3 | 315 | 250 | 350 | 285 | 225 | 300 |
Mxxx-12503150 |
3 | 376 | 250 | 350 | 315 |
250 |
350 |
Mxxx-12503600 |
3 | 428 | 300 | 400 | 360 | 250 | 350 |
Mxxx-12504100 |
3 | 480 | 330 | 450 | 410 |
300 |
400 |
Mxxx-12504600 |
3 | 532 | 370 | 500 | 460 | 330 |
450 |
690 V (500 V to 690 V +/-10%
Product Code M600/M700/M701/M702 |
Normal Duty | Heavy Duty | |||||
Supply Phases | Max Cont. Current (A) |
Motor Power (kW) |
Motor Power (HP) |
Max Cont. Current (A) |
Motor Power (kW) |
Motor Power (HP) |
|
Mxxx - 07600190A |
3 | 23 | 18.5 | 25 | 19 | 15 | 20 |
Mxxx - 07600240A |
3 | 30 | 22 | 30 | 24 | 18.5 | 25 |
Mxxx - 07600290A |
3 | 36 | 30 | 40 | 29 | 22 | 30 |
Mxxx - 07600380A |
3 | 46 | 37 | 50 | 38 | 30 | 40 |
Mxxx - 07600440A |
3 | 52 | 45 | 60 | 44 | 37 | 50 |
Mxxx - 07600540A |
3 | 73 | 55 | 75 | 54 | 45 | 60 |
Mxxx - 08600630A |
3 | 86 | 75 | 100 | 63 | 55 | 75 |
Mxxx - 08600860A |
3 | 108 | 90 | 125 | 86 | 75 | 100 |
Mxxx - 09601040A |
3 | 125 | 110 | 150 | 104 | 90 | 125 |
Mxxx - 09601310A |
3 | 150 | 132 | 175 | 131 | 110 | 150 |
Mxxx - 09601040E |
3 | 125 | 110 | 150 | 104 | 90 | 125 |
Mxxx - 09601310E |
3 | 155 | 132 | 175 | 131 | 110 | 150 |
Mxxx - 10601500E |
3 | 172 | 160 | 200 | 150 | 132 | 175 |
Mxxx - 10601780E |
3 | 197 | 185 | 250 | 178 | 160 | 200 |
Mxxx - 11602100E |
3 | 225 | 200 | 250 | 210 | 185 | 250 |
Mxxx - 11602380E |
3 | 275 | 250 | 300 | 238 | 200 | 250 |
Mxxx-12603150 |
3 | 376 | 355 | 450 | 315 | 280 | 400 |
Mxxx-12603600 |
3 | 428 | 400 | 500 | 360 | 355 | 450 |
Mxxx-12604100 |
3 | 480 | 450 | 600 | 410 | 400 |
500 |
Mxxx-12604600 |
3 | 532 | 500 | 650 | 460 | 450 | 600 |