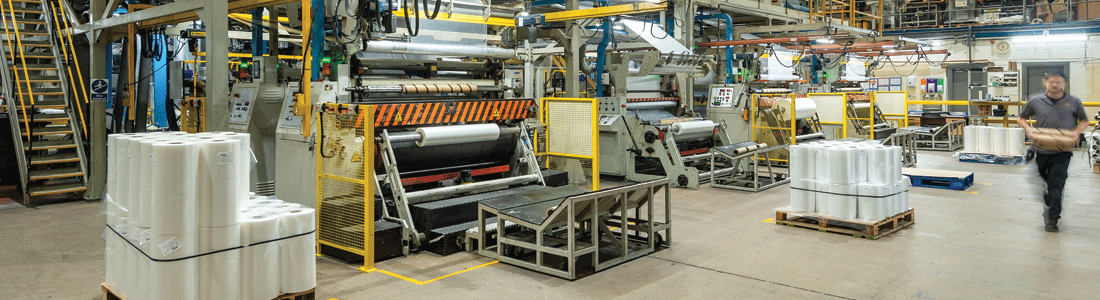
The challenge
BPI Packaging Solutions is a manufacturer of flexible packaging film, with seven sites across the UK and Romania. The Winsford, UK site produces innovative, sustainable film used in various applications from NHS PPE to surgical waste bags. The facility has two engineers on-site, so occasionally outsources motor repairs to Rewinds & J. Windsor.
Recently in a bid to be more efficient and overcome ongoing maintenance challenges, the company decided to convert all DC motors to AC on their 25-year-old main blown film extruder – the heart of the machine.
The solution
BPI Packaging Solutions and Rewinds & J. Windsor chose M700 for the job. Two extruders were all converted to Unidrive, Dyneo and Tec solutions.
Apostolos Papadopoulos, Area Sales Manager UK North West for Control Techniques, said: “By swapping to AC, the customer benefits from 30% energy saving, lower maintenance cost and improved machine performance. We installed one TEC motor, and the comparison between that and the Dyneo solution highlighted the better performance of the Dyneo, in a smaller size and with minimum maintenance requirements.”
The benefits
“The Control Techniques’ drives are brilliant. We have all the benefits associated with switching from DC to AC, and, as a result, we are now converting to Control Techniques drives across the site to keep all parts uniform. Replacement drives will be readily available and easy to source, solving the challenges we faced with the old drives. The service we have received from Control Techniques has been great; certainly not your typical pushy sales teams!” Rob McAloon, Engineering Manager for BPI Packaging Solutions.
Read the full case study:
Impressed? Contact us for your automation needs