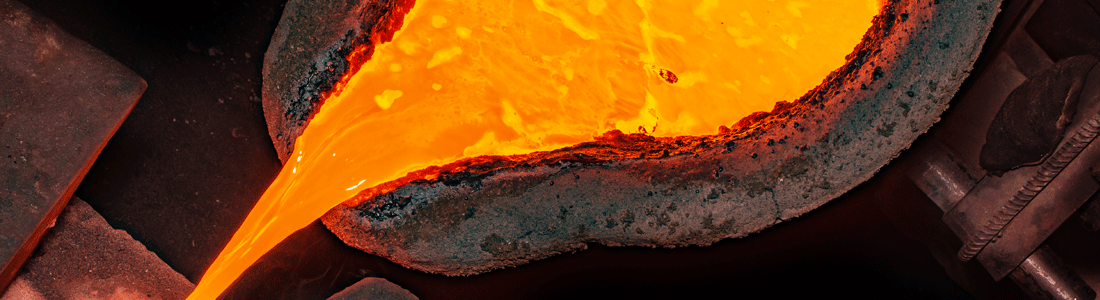
The challenge
The most significant challenge in deploying electrical motors in a vacuum environment is avoiding the possibility of corona arcing between electrical conductors. As vacuum levels reduce air pressure within the environment, the rarefied air atmosphere will easily ionize, creating a corona arc that allows current to flow between unprotected high voltage conductors. Once the arc begins, motor winding insulation erodes and results in turn-to-turn short circuits that render the motor winding damaged, thus necessitating replacement of the motor.
In order to prevent damage to the motor and extend its life the voltage applied must be controlled to levels below the application’s Corona Inception Voltage (CIV), a value derived from the pressure and composition of surrounding air.
The solution
Despite the challenges of deploying a casting mold servo positioning system in a vacuum environment, Applied Motion Systems was able to do just that with a high degree of confidence thanks to the flexibility and reliability of Control Techniques Unidrive M700 drives. After calculating a maximum DC bus voltage of 63 volts to prevent corona arcing within the environment, AMS assessed multiple drive platforms and found that only Control Techniques offered standard drives capable of operating under this non-standard voltage limit.
Not only did these drives satisfy the most arduous requirement of the project, they came with a slew of other benefits like compatibility with a semi-customized servo motor with resolver feedback, high-quality position control, flexibility across motor types, and easily integrated “PLC Controlled Motion”. When it comes to unique and demanding applications such as these, Applied Motion Systems knows to look no further than Control Techniques.
The benefits
“Implementing position control of Unidrive M700 drives with a third party PLC turned out to be a streamlined, user friendly process that required minimal effort thanks to Control Techniques’ PLC Controlled Motion.”
Systems Engineer Applied Motion Systems, Inc
Read the full case study:
Impressed? Contact us for your automation needs