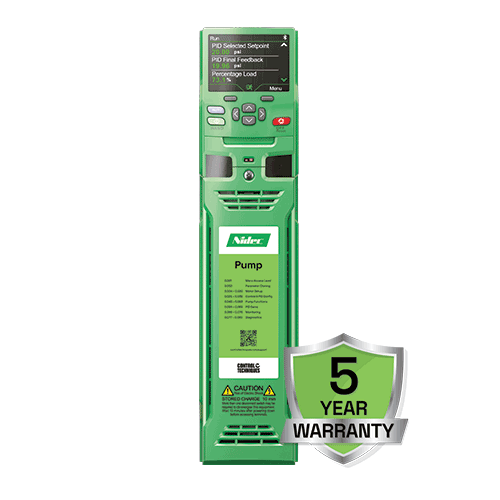
- Overview
- Specifications
- Options
- Downloads
Simple, reliable flow control
Applications involving the flow of water demand extreme reliability and low energy consumption. Available in IP20 and IP65 packages, Control Techniques’ F600 drive, part of the newly introduced Specialist series of industry-specific drive technologies, builds on our company’s five decades of drives expertise, delivering precise, dependable flow control.
Everything you need is baked into the drive itself. The F600 packs all of the features you’ll need, presented using terminology you’ll understand. This isn’t a generic drive with pump features tacked on; it’s a dedicated, specialist pump drive, designed from the ground up to deliver the reliability and efficiency you need.
Introducing the specialist Pump Drive
The perfect mix of application-specific features developed into a single solution
![]() The F600 drive is tuned to suit your every need, optimised for minimal setup time yet sacrificing none of the flexibility. Whatever the challenge, our dedicated approach to clear parameter naming and structuring ensures we not only have the answers, but in a format you’ll understand. |
|
![]() On average, 85% of a pump’s life-cycle cost is attributed to its energy consumption, therefore, optimising the energy usage can mean a significant reduction in the total cost of ownership. The F600 drive thrives on delivering more efficient ways of operating your variable torque application. You’ll see the benefits in reduced running costs and lower energy requirements. |
|
![]() The F600 can also control the most efficient motors available, meeting IE5 efficiency levels, such as the Nidec Leroy Somer Dyneo+ hybrid permanent-magnet motor. With all of this combined, the F600 is your best choice to save you money every day. |
|
![]() The F600 Pump Drive offers a host of dedicated features including dry-run prevention, pipe fill, pump cleaning, over-cycling protection and level switch control. A range of different control modes covering single pumps and also different parallel pump configurations make Control Techniques’ F600 a truly versatile solution. |
High power drives - whatever the size of your pump, we can control it.
Highly efficient pre-engineered motor control system
Control Techniques knows that reliability and efficiency are game changers for pump systems. Either a standalone compact product to fit in your existing system or a Free Standing Drive with a small footprint will support to optimise your motor efficiency.
Light weight, but no light weight!
The F600 is available with Control Techniques' larger frames too, which not only offer 500 kW of power in a single module, and 130 kg is up to 60 kg lighter than competitor drives, but its small footprint, only 295 mm width, and pre-engineered accessories make it easy to install even in a 400mm wide panel or retrofit in industry-standard cubicles.
No extra engineering required
The DFS Series High Power Freestanding Drives is a pre-assembled cabinet that fits in reduced space with all necessary system components included. However, flexibility is a strong point here, and understanding that every system requests your own configuration, we are happy to integrate: load switch, fuses, fan, line and sharing chokes or filters as your specifications require. The cabinet can also come with a door mounted HMI with Real-Time Clock, for easy set-up and maintenance.
Thanks to the dedicated online configurator, getting a quote and ordering is as simple as can be. Furthermore, we can ship your Freestanding drive to you with a very short lead time, saving weeks on typical industry standards.
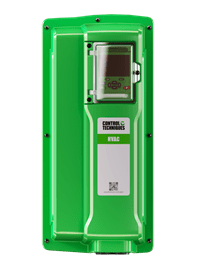
Pump Drive F600 IP65
The Pump Drive F600 offers a full IP65 solution with exactly the same dedicated pump features & capabilities as the standard models.
IP65 provides protection from total dust ingress and low pressure water jets from any direction, making it a simple choice for harsh environments and the outdoors*. The Pump Drive F600 is now one of the most protected drives on the market, maximising pump uptime and productivity, while cutting maintenance costs.
Standard and High IP drives
The High IP drive will already be familiar to users of the F600, with all the same features that make commissioning effortless. The Hand-Off-Auto keypad with the built-in real-time clock is still available, sealed, and the protective casing has been designed with easy servicing and usability in mind. This new variant enables customers to use both standard and high IP drives for the same project, so there is no longer any headache with mixing-and-matching vendors or product feature sets, making project qualification straightforward.
Save on installation
The F600 High IP drive is enclosed in a sturdy, protective yet light casing, providing a compact solution. This not only allows easy integration in harsh environments but wall mounting close to the pump reduces installation costs, through:
- No cabinet required
- Shorter cable lengths
- Less labour time/cost to install drive
Features
Unmatched total cost of ownership, with innovative protective features and extended equipment life
The F600 has comprehensive pump and motor protection features which minimise unplanned downtime, improving overall effectiveness and guaranteeing better value for money. Bring true resilience to your application and easily ride-through component failures.
Automatic error recovery
In the unlikely event of detecting an error with your pump, the F600 has the ability to dynamically recover and resume normal operation.
Limit protection
If the feedback exceeds the limits defined for your application, the F600 has the ability to raise an alarm or stop the drive to protect your equipment and preserve its lifetime.
Transducer loss protection
In the event of losing connection to the transducer, the F600 can stop, continue to run at a fixed speed or ignore the fault depending on the application requirements.
Fire mode
Fire mode allows the drive to disable all trips and to continue to run uninterrupted during emergency events if the application requires.
Save on energy through a wide range of energy features
The F600 is 98% efficient, meaning very little energy is lost in power conversion.
Even more, the real savings potential gets unlocked by the F600’s built-in features that can further reduce energy consumption:
Low load savings
The F600 helps maximise energy savings when demand is low. Activing Control Techniques’ leading-edge Low Load Power Saving function, the drive dynamically reduces the voltage applied to reduce losses in the motor and make the system more efficient.
Sleep mode
When demand falls below a specified set-point the drive will automatically enter sleep mode and restart itself once demand rises above the set-point. Not only does this greatly reduce the amount of energy consumed, it also saves on equipment wear to preserve its lifetime.
The F600 features optimised control for your flow applications
Pipe fill
Prevent spikes in pressure at start-up using a controlled ramp, to protect your piping system and the pump itself.
Dry-run prevention
Prevent the pump running dry by checking the load against a threshold; with flexible configurations to dynamically adjust output, set an alarm or stop the drive.
Over-cycling protection
Optimise drive, motor and pump sizing, and regulate pump wear by limiting the number of start-stops per hour. Flexible configurations allow to dynamically alter cycling reference limits, set an alarm or stop the drive when a limit is reached.
No-flow detection
Where there is no-flow or low-flow, the F600 drive can automatically enter sleep mode to save energy, based on the feedback of a pulsed flow transducer, or triggered by a flow switch, or detected by the software alone.
Cleaning
Live, continuous monitoring of the system is used to trigger an automatic drive-based cleansing cycle to clear the pump impeller and help avoid maintenance costs on cleaning pump blockages.
Level switch control
Level switches provide critical protection for tanks in the event of the level reaching a “high” switch, whereby the pump is stopped, or a “low” switch, whereby the pump is started, to ensure pumping within tank levels.
Pump control modes | flexible support for every system
Single pump
Control Techniques’ Single Pump mode is an effective and versatile variable speed control solution for maintaining a constant set-point in a single pump configuration.
- Fire mode allows the drive to disable all trips and to continue to run uninterrupted during emergency events if the application requires
Cascade
Cascade mode allows the F600 to operate with up to 4 assist pumps to aid the primary pump when required.
- Energy usage is optimised whereby the assist pumps are only enabled when demand reaches sufficient levels.
- Assist pumps are used alternately to apply uniform wear and increase pump availability.
- Over-cycling protection for assist pumps to control the number of starts and stops per hour.
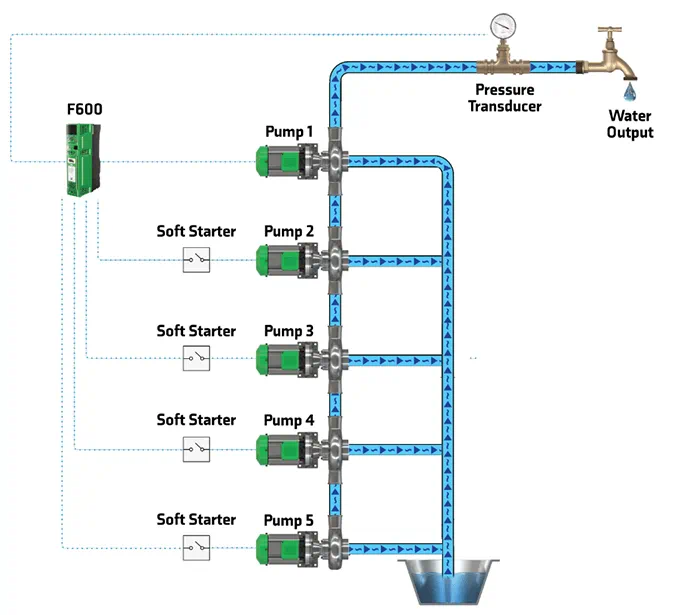
Multi-leader
Complete control of your application with up to 3 x F600 drives and maximum energy savings with these variable frequency drives running parallel.
- The Multi-leader drive configuration provides redundancy and removes the need for a PLC
- The “lead” drive is automatically cycled to apply uniform wear
- If the “lead” drive loses its transducer, it can access the transducer feedback from another F600 in the system over Ethernet
- Dynamic re-selection of “lead” pump if a pump is taken out of service or develops a fault
Download the brochure for detailed features and specifications
Software
![]() Connect is our latest drive configuration tool for commissioning, optimising and monitoring drive/system performance. Download |
This product comes with 5-year warranty as standard
No registration. No extra cost. Just peace of mind from day one. Learn more.
Pump Drive F600 ratings guide
200/240 Vac ±10%
Drive | Normal Duty |
||
Max continuous current (A) |
Motor shaft |
Motor shaft power (hp) |
|
F600-03200066A10 |
6.6 |
1.1 |
1.5 |
F600-03200080A10 |
8 |
1.5 |
2 |
F600-03200110A10 |
11 |
2.2 |
3 |
F600-03200127A10 |
12.7 |
3 |
3 |
F600-04200180A10 |
18 |
4 |
5 |
F600-04200250A10 |
25 | 5.5 | 7.5 |
F600-05200300A10 |
30 | 7.5 | 10 |
F600-06200500A10 |
50 | 11 | 15 |
F600-06200580A10 |
58 | 15 | 20 |
F600-07200750A10 |
75 | 18.5 | 25 |
F600-07200940A10 |
94 | 22 | 30 |
F600-07201170A10 |
117 |
30 |
40 |
F600-08201490A10 |
149 |
37 |
50 |
F600-08201800A10 |
180 |
45 |
60 |
F600-09202160A10 |
216 |
55 |
75 |
F600-09202660A10 |
266 |
75 |
100 |
F600-09202160E10 |
216 |
55 |
75 |
F600-09202660E10 |
266 |
75 |
100 |
F600-10203250E10 |
325 |
90 |
125 |
F600-10203600E10 |
360 |
110 |
150 |
380/480 Vac ±10%
Drive |
Normal Duty |
||
Max continuous current (A) |
Motor shaft power (kW) |
Motor shaft power (hp) |
|
F600-03400034A10 |
3.4 | 1.1 |
1.5 |
F600-03400045A10 | 4.5 |
1.5 |
2 |
F600-03400062A10 | 6.2 |
2.2 |
3 |
F600-03400077A10 |
7.7 |
3 |
5 |
F600-03400104A10 |
10.4 |
4 | 5 |
F600-03400123A10 |
12.3 | 5.5 | 7.5 |
F600-04400185A10 |
18.5 |
7.5 |
10 |
F600-04400240A10 |
24 |
11 |
15 |
F600-05400300A10 |
30 |
15 |
20 |
F600-06400380A10 |
38 |
18.5 |
25 |
F600-06400480A10 |
48 |
22 |
30 |
F600-06400630A10 |
63 |
30 |
40 |
F600-07400790A10 |
79 |
37 |
50 |
F600-07400940A10 |
94 |
45 |
60 |
F600-07401120A10 |
112 |
55 |
75 |
F600-08401550A10 |
155 |
75 |
100 |
F600-08401840A10 |
184 |
90 |
125 |
F600-09402210A10 |
221 |
110 |
150 |
F600-09402660A10 |
266 | 132 |
200 |
F600-09402210E10 |
221 | 110 |
150 |
F600-09402660E10 |
266 | 132 |
200 |
F600-10403200E10 |
320 |
160 |
250 |
F600-10403610E10 |
361 |
200 |
300 |
F600-11404370E10 |
437 |
225 |
350 |
F600-11404870E10 |
487 |
250 |
400 |
F600-11405070E10 |
507 |
280 |
450 |
F600-12404800TU0 |
608 |
315 |
500 |
F600-12405660TU0 |
660 | 355 |
550 |
F600-12406600TU0 |
755 |
400 |
650 |
F600-12407200TU0 |
8651 |
500 |
700 |
Note1: 110 % Overload at 30ËšC and below and No Overload above that.
500/575 Vac ±10%
Drive |
Normal Duty |
||
Max continuous current (A) |
Motor shaft power (kW) |
Motor shaft power (hp) |
|
F600-05500039A10 |
3.9 |
2.2 |
3 |
F600-05500061A10 |
6.1 |
4 |
5 |
F600-05500100A10 |
10 |
5.5 |
7.5 |
F600-06500120A10 |
12 |
7.5 |
10 |
F600-06500170A10 |
17 |
11 |
15 |
F600-06500220A10 |
22 |
15 |
20 |
F600-06500270A10 |
27 |
18.5 |
25 |
F600-06500340A10 |
34 |
22 |
30 |
F600-06500430A10 |
43 |
30 |
40 |
F600-07500530A10 |
53 |
37 |
50 |
F600-07500730A10 |
73 |
45 |
60 |
F600-08500860A10 |
86 |
55 |
75 |
F600-08501080A10 |
108 |
75 |
100 |
F600-09501250A10 |
125 |
90 |
125 |
F600-09501550A10 |
155 |
110 |
150 |
F600-09501250E10 |
125 |
90 |
125 |
F600-09501500E10 |
150 | 110 | 150 |
F600-10502000E10 |
200 | 130 | 200 |
F600-11502480E10 |
248 | 175 | 250 |
F600-11502880E10 |
288 | 225 | 300 |
F600-11503150E10 |
315 | 250 | 350 |
F600-12503150 |
376 | 250 | 350 |
F600-12503600 |
428 | 300 | 400 |
F600-12504100 |
480 | 330 | 450 |
F600-12504600 |
532 | 370 | 500 |
500/690 Vac ±10%
Drive |
Normal Duty |
||
Max continuous current (A) |
Motor shaft power (kW) |
Motor shaft power (hp) |
|
F600-07600230A10 |
23 |
18.5 |
25 |
F600-07600300A10 |
30 |
22 |
30 |
F600-07600360A10 |
36 |
30 |
40 |
F600-07600460A10 |
46 |
37 |
50 |
F600-07600520A10 |
52 |
45 |
60 |
F600-07600730A10 |
73 |
55 |
75 |
F600-08600860A10 |
86 |
75 |
100 |
F600-08601080A10 |
108 |
90 |
125 |
F600-09601250A10 |
125 |
110 |
150 |
F600-09601500A10 |
150 |
132 |
175 |
F600-09601250E10 |
125 |
110 |
150 |
F600-09601550E10 |
155 |
132 |
175 |
F600-10601720E10 |
172 |
160 |
200 |
F600-10601970E10 |
197 |
185 |
250 |
F600-11602250E10 |
225 |
200 |
250 |
F600-11602750E10 |
275 |
250 |
300 |
F600-11603050E10 |
305 |
280 |
400 |
F600-12603150 | 376 | 355 | 450 |
F600-12603600 | 428 | 400 | 500 |
F600-12604100 |
480 | 450 | 600 |
F600-12604600 |
532 | 500 | 650 |
Normal duty operation only
Suitable for pump applications, with a current overload requirement of 110% for 60 s*.
Conformance
- IP20 / NEMA1 / UL TYPE 1 *UL open class as standard, additional kit needed to achieve Type 1
- IP65 / NEMA4 / UL TYPE 12 rating is achieved on the rear of the drive when through panel mounted
- *Frame size 9D, 9E, 10D and 10E achieve IP55 / NEMA 4 / UL Type 12
- Ambient temperature -20 °C to 40 °C (-4 °F to 104 °F) as standard. Up to 55 °C (131 °F) with derating
- Humidity 95 % maximum (non-condensing) at 40 °C (104 °F)
- Altitude: 0 to 3000 m (9900 ft), derate 1 % per 100 m (330 ft) between 1000 m (3300 ft) and 3000 m (9900 ft)
- Random Vibration Tested in accordance with IEC 60068-2-64
- Bump Tested in accordance with IEC 60068-2-29
- Sinusoidal Vibration Tested in accordance with IEC 60068-2-6
- Mechanical Shock Tested in accordance with IEC 60068-2-29
- Storage temperature -40 °C to 55 °C (-40 °F to 131 °F) or up to 70 °C (158 °F) for short-term storage
- Electromagnetic Immunity complies with EN 61800-3 and EN 61000-6-2
- With onboard EMC filter, emissions comply with EN 61800-3 (category C3)
- EN 61000-6-3 and EN 61000-6-4 with optional footprint EMC filter
- IEC 60146-1-1 Supply conditions (category C1 or C2 depending on rating)
- IEC 61800-5-1 (Electrical Safety)
- IEC 61131-2 I/O
- EN 61000-3-12 with optional line reactor
- UL 508C (Electrical Safety)
Dimensions
Frame size |
Dimensions | Weight |
|
mm (HxWxD) |
in (HxWxD) |
kg (lb) |
|
3 | 382 x 83 x 200 |
15.0 x 3.3 x 7.9 |
4.5 (9.9) |
4 | 391 x 124 x 200 |
15.4 x 4.9 x 7.9 |
6.5 (14.3) |
5 | 391 x 143 x 200 |
15.4 x 5.6 x 7.6 |
7.4 (16.3) |
6 | 391 x 210 x 227 |
15.4 x 8.3 x 8.9 |
14 (30.9) |
7 | 557 x 270 x 280 |
21.9 x 10.6 x 11.0 |
28 (61.7) |
8 | 803 x 310 x 290 |
31.6 x 12.2 x 11.4 |
50 (110.2) |
9A | 1108 x 310 x 290 |
43.6 x 12.2 x 11.4 |
66.5 (146.6) |
9E/10E | 1069 x 310 x 290 |
42.1 x 12.2 x 11.4 |
46 (101.4) |
9D/10D |
Rectifier |
Rectifier 15.8 x 12.2 x 11.4 ----------------------- Inverter 30.4 x 12.2 x 11.4 |
|
11E |
1242 x 310 x 312 |
48.9 x 12.2 x 12.3 |
63 (138.9) |
12 |
1750 x 295 x 526 |
68.9 x 11.6 x 20.7 |
AC to AC ('T' type): 130 kg (287 lb) DC to AC ('D' type): 113 kg (249 lb) |
*For more detailed information please see technical documents.