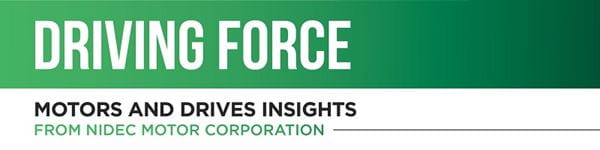
BLDC motors in autonomous guided vehicles (AGVs) - Part 1 of 2
AGVs offer significant benefits for commercial and industrial applications
August 2018
With the terms Industry 4.0 and Industrial Internet of Things (IIoT) now concrete realities, robotic automation has evolved past its humble origins. Autonomous guided vehicles (AGVs) are an innovative class of products helping streamline the industrial automation process. AGVs can be ideal for applications such as warehouse storage and retrieval, manufacturing, product assembly and material handling. They offer benefits like reduced human personnel costs, decreased risk of injuries and increased efficiency.
Arthur “Mac” Barret is credited with producing the first AGV in 1953, when he developed a towing tractor pulling a trailer around a grocery store via an overhead wire.(1) AGVs have come a long way since that original system Barrett called a driverless vehicle. During the 1970s, car manufacturer Volvo built a more efficient assembly system using AGVs rather than the more conventional conveyor line. This was so successful that Volvo actually started selling their AGVs to other auto manufacturers.
Early AGVs used fairly simple methods of navigation. Today’s AGVs are much more advanced and flexible than ever before. Laser- and camera-guided navigation is often used for modern AGVs,(2) which are becoming increasingly popular in a relatively short period of time. Some estimates indicate that certain large retailers have increased their use of AGVs by as much as 1,500% in just a few years.(3) That’s a tremendous increase – and it seems likely that this number will only continue growing as more companies increase their automation processes.
Many other companies are riding this rising tide of industrial automation, developing AGVs well-suited for their applications. One important consideration when designing the systems that control these AGVs is deciding which type of motor can best power them. In many cases, brushless DC motors (BLDC motors) can be an optimal choice because of the versatility, reliability and efficiency they offer.
Versatility of BLDC motors in AGV applications
Versatility is one of the biggest advantages that BLDC motors can offer in AGV applications. They can provide the ability to adapt a motor technology to form factors that are tailored to the specific needs of the customer. One example of brushless DC being a flexible motor technology is that it can turn inside out more easily than other motor technologies to better suit an application.
Nidec Motor Corporation’s Director of Engineering, William Moore, recently shared some of his thoughts on using BLDC motors in automated guided vehicle applications. “What every AGV has in common is that they have wheels. In some applications, you drive the wheel in a conventional way where the motor sits outside the wheel. When we talk about an outer rotor format, however, you can have the motor sit inside the hub of the wheel. It almost appears as if it becomes one component, with the wheel and motor resembling one part, which gives the AGV designer much more flexibility in terms of space usage.” This space savings can be an advantage for the original equipment manufacturer (OEM).
Reliability another key factor
BLDC motors can be well-suited to meet the customer’s requirements for AGV applications because of the sheer reliability they provide. As suggested by the name, brushless DC motors eliminate the need for brushes, which experience wear and tear over a brushed motor’s life. If an OEM has a long life specified for the drive, a brushed motor needs to have serviceable brushes. These come with the necessity of scheduled maintenance, which translates to downtime when the motor’s brushes have to be serviced.
Designers further need to factor in things like wear debris, something that can be detrimental in a clean environment where you don’t want to worry about the wear that’s associated with brushes. Other important considerations when designing for a clean environment are the noise and sound signature associated with brushes. They tend to carry increased sound level inherently. Going with a BLDC motor can help minimize these concerns.
BLDC motor efficiency pays dividends
Brushless DC motors offer high efficiency across a range of speeds. Brushed DC motors don’t typically operate at low speeds, making it difficult to obtain lower speed stability with them. With brushless DC motors, on the other hand, operation at low speeds is fairly simple. According to Moore, “You want to operate at a low speed with BLDC motors? No problem. You design the motor to do it, and it’s not a big deal. Or if you want to go with a really high speed and couple it with a gearbox, no problem. High speed is not going to accelerate the wear on brushes or anything like that. BLDC can be an ultra-flexible technology to deliver variable speed.”
Increased battery efficiency is another advantage provided by BLDC motors. Since BLDCs can operate with greater efficiency, they also benefit from longer battery life. This increased battery life comes both in terms of the usable life of the battery and in terms of the time between battery charging cycles. The more efficient a motor is, the more time an AGV can spend doing the work it was designed to do rather than sitting idle while being charged.
As Moore pointed out, “There’s no value to anybody for the AGV to spend time charging. That just means more AGVs you have to put out there to do the work to cover the ones that are charging. So BLDC motor efficiency tends to pay dividends. We sometimes see engineers attempt to save money up front by designing a motor with lower efficiency. What we've seen is that oftentimes it’s very hard to justify reducing costs of the motor by sacrificing efficiency in the hopes it will pay for itself in the long run. The reality is that the cost of poor efficiency can trump whatever initial costs were saved by creating a less-efficient motor.”
In Part Two of “BLDC Motors in Autonomous Guided Vehicles (AGVs),” we’ll discuss more considerations such as envelope constraints, manufacturability and product testing.
Sources:
(1) “Let’s remember Mac Barrett, father of the AGV.” Modern Materials Handling. https://www.mmh.com/article/lets_remember_mac_barrett_father_of_the_agv (Accessed on August 24, 2018.)
(2) “AGVs: Predictably Flexible.” Modern Materials Handling. https://www.mmh.com/article/agvs_predictably_flexible (Accessed on August 24, 2018.)
(3) “Automatic Fast Charging of Automated Guided Vehicles (AGVs).” AZO Materials. https://www.azom.com/article.aspx?ArticleID=15531 (Accessed on August 24, 2018.)