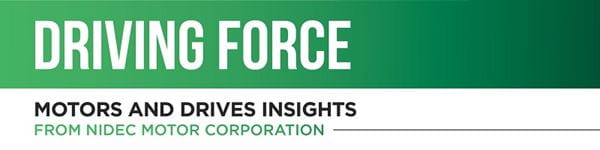
Automation helps drive next generation of farming
February 2019
The past few years have seen a rapidly increasing trend toward automation in many walks of life from home to business. This automation trend has been embraced by the agricultural industry as one viable solution for the shrinking labor pool impacting farmers. As with any developing trend, there are several factors behind this increasing demand for agricultural automation.
In general, farmers spend over 30% of their annual budget on labor costs alone. Despite factoring this into their budgets, farmers are struggling each year to find enough workers. Even in cases where farmers offer significantly higher-than-usual wages, many report they can’t find enough skilled workers to handle their labor demands. Farmers and agricultural corporations aren’t considering automation from a simple desire to replace workers, but to solve the problem that they often can’t find enough workers even with economic incentives like high pay.
Moving from hydraulics to electrification
Another significant factor driving agricultural automation is the trend of moving hydraulic systems to electrification. This move toward electrification has been inspired in large part by increasingly stringent environmental regulations governing diesel engines used to power hydraulic systems, like the EPA’s Tier 4 Emission standards for nonroad diesel engines. Several OEMs we spoke with reported that meeting these more stringent requirements requires them to develop larger equipment to treat exhaust fumes, because more components are needed to generate the necessary chemical reactions. Larger equipment results in doubling or even tripling the price of engines in addition to increasing their weight. Considering that space is at a premium in this type of equipment, that adds another layer of difficulty in continued use of hydraulic systems.
Some OEMs are moving to a hybrid type of equipment, where the diesel engine operates like a compressor to power some of the hydraulics that have to stay on during use. Other types of equipment that don’t require continuous operation can use electric motors and run a diesel engine-powered generator. The OEM’s objective is to reduce the size of the diesel engine so that the equipment costs less. Manufacturers can design equipment that saves consumers money by doing that, and they can also meet the regulations on pollution, because these regulations apply to larger engines.
Another important factor contributing to the move away from hydraulic systems is contamination due to hydraulic fluid leakage. Contamination sometimes requires farmers to cease harvesting fields while they remove contaminated dirt, which is time-consuming and extremely costly. According to Nidec Motor Corporation’s Senior Product Manager, Marketing/Business Development Alex Valentino, “This is what full electrification means, where there are no hydraulic lines that need to be taken from the compressor to different parts of the equipment; it’s just wires so a lot easier to deal with, as opposed to when one of those hydraulic lines burst. No matter what kind of fluid they use or how environmentally friendly it claims to be, such fluids are not healthy for the environment when a hose bursts.”
According to farmers we have talked to, they often stop work on a field that has been contaminated to hire an outside cleanup crew to treat the field. It can be a hardship in lost time, productivity and money for a farmer who has to deal with such a cleanup. Valentino said, “Cleanup companies often charge a lot, and they’re not always available right away, so you may have to wait two or three weeks for them to come out to handle the treatment. This means your fruit or other crop could rot on the trees, bushes or in the field if you can’t have the crew come in right away.”
Swarms of AGVs
With trends in the agricultural industry moving toward electrification and automation, large companies are investing more and more money into developing new technology. One new concept that seems to be very promising is called swarm farming, which utilizes autonomous guided vehicles (AGVs). Valentino described it as “…amazing. Instead of having one gigantic machine that plows through a field and comes back, you have a number of much smaller AGVs. How many AGVs are needed will depend on how big of a field they have to work on. These machines have wheels, traction motors and drives to move. They are GPS-controlled and seed each plant by the location that is recorded. They use that GPS technology to go back and tend the different plants, taking care of tasks like weed-killing and eventually harvesting.”
Companies we have spoken to who are developing this new method plan to lease the AGVs to farmers. The assumption is that most farmers would be unwilling to purchase machines that cost several hundred thousand dollars to perform a specific task. The number of AGVs needed is based on the size of each field being worked. These AGVs offer another benefit of being able to work day and night and in various temperatures. In addition to being small, some of them may have a solar panel on top and batteries inside, with everything being electric.
Another big advantage is that using a number of smaller machines would make dealing with breakdowns presumably less costly. According to Valentino, “Some of these machines are programmed so that if one machine breaks down, another can pick up the work.” This offers an obvious advantage over farmers who have one much larger machine working their fields. When a single machine like that breaks down, work grinds to a halt until the machine can be repaired or replaced. Another cost consideration to using the fleets of smaller AGVs is that it is usually cheaper to repair or replace a small machine than a much larger one.
He also stressed that machines designed to automate agricultural tasks are not always meant to replace workers entirely, but actually assist farm workers with their duties. “There are types of carts or tractors that are fully electrical, solar-powered and programmed to follow the pickers. So instead of having to haul a bunch of boxes while they pick the fruit and then take them to whatever container they need to put them in, these carts follow them everywhere they go. They just pick the crop, put it in the cart and keep going. This can help decrease wasted time and lower the risk of worker injury.”
New opportunities for skilled labor
Another benefit to this growing trend of agricultural automation is that it opens up a huge opportunity for skilled labor. Farms that become more automated will need an increased number of skilled workers who can manage that type of equipment, including fleet managers. Instead of programming and maintaining these AGVs to work in an indoor warehouse, these fleet managers will need to direct their AGVs to work and assist workers in fields and orchards.
Over-aging, farm labor shortages, food and fiber requirements of a growing world population and stringent regulatory standards are factors that will further increase the demand for agricultural automation. Pairing electric motors and drives with automated farm equipment can help solve the problem farmers face in finding enough skilled labor to work their fields. Nidec Motor Corporation offers a wealth of experience in creating automation solutions and AGVs for farming and agricultural applications. When energy efficiency and reliability are required, having a partner like Nidec Motor Corporation, with proven experience in developing the innovative technology required to solve problems like farm labor shortages, can make all the difference.
Alex Valentino is Nidec Motion Control Group’s Senior Product Manager Marketing/Business Development with more than 20 years’ experience in the motor industry. Alex specializes in servo motors and robotics. He has a degree in Mechanical Engineering from Washington University, St. Louis.