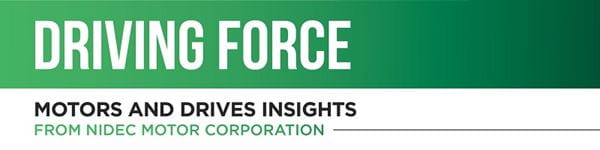
BLDC motors in autonomous guided vehicles (AGVs) - Part 2 of 2
October 2018
In Part 1 of this two-part blog series, we discussed some of the significant benefits that using brushless DC motors in automated guided vehicles (AGVs) can offer for customer requirements in commercial and industrial applications. In this second part, we’ll discuss design considerations that application and specifying engineers may wish to keep in mind, such as envelope size constraints, manufacturability and product testing.
Space constraint challenges for AGV motors
One of the typical challenges when it comes to designing BLDC motors for use in AGVs is that of space constraints. Most companies want to achieve high efficiency for their AGVs, which can be easier to achieve if you have unlimited space. In cases where the envelope is more constrained, however, high efficiency can be more difficult to achieve. Most AGVs have gearmotors (one or more) that either assist the AGV with its own locomotion or help lift and/or rotate the load being transported. Because the center of an AGV needs to remain clear for battery placement and other peripheral components, space for motion and control components can be limited.(1)
Companies are requesting smaller but more powerful motors, with higher levels of torque.(2) This is often because they’re dealing with specific size restrictions imposed by their existing warehouse, distribution or automated storage and retrieval system (ASRS) layouts.(2) That of course can place additional size constraints on the AGV and its components, such as motors and gearboxes.
William Moore, Director of Engineering – Nidec Motion Control, stresses the importance of considering how to couple components like a gearbox to the motor to achieve the specified maximum torque requirements. Typically, this must be done while maintaining the motor components, power consumption and thermal signature in a reasonable operating range, so design and application engineers need to think about how to optimize the active material in the motor. Another thing to keep in mind is that adding additional auxiliary components can increase both the complexity and cost in an already space-restricted AGV system.(3)
According to Moore, “When we design a motor with an integrated gearbox, we have to consider the interaction between those two items. What’s the optimum operating point for both the motor and the gearbox? You then want to best optimize the entire system solution. So if someone came in here strictly with an attitude of ‘Oh I’m a motor person and I’m only worried about the motor; I’m going to have a motor with a 90% peak operating efficiency’ but doesn’t really think about what’s best on the gearbox side, you can miss the opportunity to have the best optimized solution.”
Manufacturability of BLDC motors for AGVs
It can be important for engineers to think about what the customer or user is looking for as an end result. Says Moore, “Sometimes our customers come to us and say, ‘We think we want this ratio of gearbox and a motor that produces this amount of torque, and we want it to operate at this speed.’ But what we usually ask our customers is, ‘What’s the output – the amount of power and torque – that you need?’ And then we work from there to determine where the optimal motor and gear ratio is for the total envelope that’s available. We can configure the whole package to give them what we believe to be the optimal solution for their specifications.”
The design stage of creating a BLDC motor for a customer’s AGV requirements can be thought of as a partnership between the customer and the motor manufacturer. This collaboration can help contribute to an AGV system’s success.(4) A certain amount of give-and-take is usually necessary, and it can be helpful to consider the other’s viewpoint and expertise. The customer may best understand the needs for the specific application they’re attempting to address, whereas the motor manufacturer usually has greater experience when it comes to actual system implementation.(4)
A large part of what goes into making implementation successful is sheer feasibility. Sometimes people develop an exciting idea only to find out that it may not be practical to execute. According to Moore, “When we dig in a little deeper to a proposed solution, we often find it’s just not cost-effective to build. So we have to balance what technology is available and what creative solutions are available with the real-world capabilities of today’s manufacturing plants.”
It can be a delicate balancing act to weigh the architecture of the proposed motor solution against whether it’s manufacturable. As Moore says, “We strive to maintain an early engagement with our manufacturing teams and use processes like DFM, Design for Manufacturing, and DFA, Design for Assembly, to make sure we aren’t doing ourselves a disservice by creating this great solution that can’t be manufactured. We also factor in long-term quality and reliability along with keeping the product cost at a level that’s both acceptable to the customer and feasible on our own end.”
The product testing stage to help ensure versatility, reliability and efficiency
Once the design stage is completed, product testing is the next critical step. According to Moore, Nidec Motor Corporation begins with working to maintain a supply chain with components that are already proven to be of good, standard quality. “When it comes to something like a bearing, we try to use standard bearings where it can be easier to calculate the life and establish reliability when possible. When you get into some of these other spaces that we operate in that are high-volume and mature products, we often optimize things like a bearing system and customize it to the nth degree; but in the world of the AGV, our customers often need the process from concept to production to go more quickly. So having a portfolio of components and suppliers that have been pre-proven can be an advantage from the beginning.”
Moore points out that product testing involves much more than simply having a solid supply chain and components to use in the assembly process. “We like to develop a test fixture to simulate the customer application as best we can. So even though we are trying to start from known components and assembly methods, ultimately when you put all those things together, you need to test the products to make sure that you haven’t overlooked something in terms of interactions in the assembly and interactions that would occur in the customer application. Customers will also often physically test the motor in the specific application for which they’ve specified the motor. And we’ve got the ability here to do environmental testing, sound testing, reliability testing, electromagnetic interference testing, performance testing, just a wide array of component level testing.
“We offer the option to emulate the customer’s specified usage profile and load profile. We actually have the ability to – in the case of AGVs that operate off of batteries – use battery emulators that can simulate the charge and discharge cycle of the battery, taking into account regenerative energy that the motors produce when they’re in the application and giving energy, or converting mechanical energy back into electrical energy that charges the batteries. We can simulate these various types of application factors in our application-based testing.”
An extensive product testing stage can be a huge value-add for customers who choose to take advantage of it. Unlike Nidec Motor Corporation, not every motor manufacturer provides the same life test resources. An extra layer of simulated application level testing can help ensure that a product meets the specifications provided by a customer. This helps further improve the chance that a BLDC motor a customer intends to use in AGV applications offers versatility, reliability and efficiency.
Sources:
1. “Gearmotors on the move: Driving AGVs” Design World. https://www.designworldonline.com/gearmotors-move-driving-agvs/ (Accessed on September 10, 2018.)
2. “3 new trends in motors for packaging machines.” Packaging Digest. https://www.packagingdigest.com/machinery-parts/3-new-trends-in-motors-for-packaging-machines-2018-07-27 (Accessed on September 10, 2018.)
3. “How Sensors Are Moving Materials Handling Toward Safe Automation, Part 2.” EPS News. https://epsnews.com/2018/06/12/sensors-moving-toward-safe-automation/ (Accessed on September 10, 2018.)
4. “Guidelines for Successful Systems.” Savant Automation Website. http://www.agvsystems.com/guidelines-successful-systems/ (Accessed on September 10, 2018.)